Seamless steel tube rolling process
Following the cyclic tube rolling process, a variety of tube rolling processes have appeared in the world. Including Erhard tube rolling, automatic tube rolling, Diesel tube rolling, three-roll tube rolling, hot extrusion tube, continuous rolling tube, cold drawn (rolled) tube, hot expanded tube, etc. 8 kinds of tube rolling processes. Now they are introduced separately.
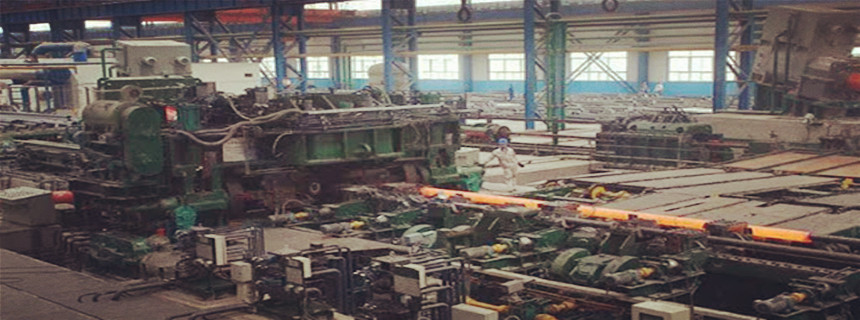
1 Ehrhardt tube rolling process
Erhard invented the hydraulic punching process in 1891 to produce punched cup-shaped blanks, and in 1899 completed the method of using a mandrel to push the punched blanks through a series of rings with gradually reduced diameters to produce seamless steel pipes. . Usually referred to as the pipe jacking process.
Nowadays, the super large diameter seamless steel pipe is still produced by the pipe jacking method, and the maximum diameter can reach 1 066 mm. In the 1980s, Mannesmann developed this process into a CPE process, mainly producing small and medium diameter seamless steel pipes.
2 Automatic tube rolling process
After Stiefel obtained the patent of the disc piercing machine in 1895, the first automatic tube rolling mill was put into production in the United States in 1903, and in 1905, the automatic tube rolling mill with an equalizer was born. The automatic tube rolling mill is also called the Steiffer tube rolling mill. After that, the automatic rolling mill became the main unit for producing seamless steel pipes.
3 Diesel tube rolling process and Accu Roll tube rolling process
Sam Diescher first conceived to introduce the rotating guide plate into the two-high cross-rolling mill instead of the original guide plate to extend the tube, and in 1932 the first Diescher tube rolling mill was born. Half a century later, the American AS company first introduced the tapered roll into the skew tube mill and obtained a patent. In 1989, the world's first Accu Roll tube mill was put into production in Yantai, my country.
4 Three-roll tube rolling process
This is a three-roll skew tube rolling process in which the capillary tube is rolled and stretched between the mandrel and 3 rolls. The three-roll tube mill is also called Assel tube mill.
5 Hot extrusion tube process
Long before the Mannesmann brothers invented the cross-rolling piercing, there was already a patent for the production of seamless steel pipes by using hot-extruded aluminum. However, it was only after the successful adoption of glass lubricants in the 1950s that the hot extrusion process of steel pipes gained real application and rapid development. Modern hot-extruded steel pipe technology is mainly used for the production of high-alloy difficult-to-deform pipes and special-shaped pipes.
6 Continuous tube rolling process
As early as 1891, the Kellogg steel pipe factory in the United States had obtained the patent for the continuous rolling mill. However, due to many technical reasons, this process has not been truly successful. It was not until the 1950s that this process achieved great development, and gradually became the dominant rolling mill for the production of seamless steel pipes with its high production capacity, high efficiency and high quality.
Looking at the above-mentioned various tube rolling processes, they were born in different periods and have been continuously improved and developed their own characteristics to meet the market's requirements for product specifications, varieties, quality and different batches. And in different periods, various seamless steel pipe production methods have been successively formed. The current research and development of the three-roll planetary rolling mill (PSW) and the piercing mill tube rolling process (CPS) show that the world is still exploring new tube rolling processes.
7 Cold drawn (rolled) tube process
In order to expand, supplement and improve the variety and quality of hot-rolled seamless steel pipes, the secondary processing technology of pipes-cold drawing (rolling) and hot pipe expansion technology has also been developed accordingly.
The cold drawing process has been used for the secondary processing of welded pipes long before the production method of hot-rolled seamless steel pipes was adopted. The cold rolling process was patented by Tabl Reduing Company of the United States in 1931. It adopts the deformation process of a similar cycle pipe rolling mill (frame reciprocating motion, multi-pass deformation), so it is also called cold Pilger pipe rolling mill.
The cold drawing (rolling) method can not only produce products with specifications and high-quality requirements that are difficult (or uneconomical) or impossible to produce by hot-rolling methods, but also can replace hot rolling to produce small-sized steel pipes and high-quality products. Special varieties (such as bearing tubes, stainless steel tubes, etc.). At present, my country's cold drawn (rolled) products account for about 20% of the total output of seamless steel pipes, which is much higher than the output of the United States, Japan, Russia and other countries.
8 Thermal expansion process
The hot expansion pipe process is the main method for producing large-diameter seamless steel pipes. There are three types of roll (cross-rolling), stretch-expanded and push-type. The maximum diameter of the roller expansion pipe can be up to 1 500mm, which is suitable for large-scale production. The push-type pipe expansion equipment is simple, low investment and low output, and is only suitable for small batch production.
There are 36 sets of seamless steel pipe hot-rolled finished product lines in our country, and there are also several sets of cold rolling (drawing) pipe lines. Among them, the hot-rolled tube mills include continuous tube rolling mills, automatic tube rolling mills, periodic tube rolling mills, precision tube rolling mills (Accu Roll), disc tube rolling mills (Diescher), three-roll tube rolling mills, tube expanding mills, top Nine categories of tube units and extruded tube units. Industrial trials of the three-roll planetary rolling mill have also been conducted. There are also more than 100 sets (sets) of equipment (mainly piercing machines) for producing seamless capillary tubes, which is more than any country in the world. It can be described as a museum of seamless steel pipe production lines in the world.
The basic process for the production of hot-rolled seamless steel pipes today is: blank preparation → heating → piercing (punching) holes → reheating the rolled pipe → sizing → finishing, inspection, testing (cooling, straightening, cutting (saw) head, sampling , Flaw detection, water pressure, weighing, anti-corrosion, etc.)→packaging and storage.
The main thermal deformation processes are piercing (punching) holes, rolling pipes and sizing (reducing) diameter. Piercing (punching) is mainly to turn a solid tube into a hollow tube; rolling tube is mainly to reduce and control the wall thickness, and it is also the main process of longitudinal extension and deformation; fixed (reduction) diameter is mainly to reduce and control outside The diameter can also be adjusted (tension reducing).
Because the pipe rolling process is not only the main process of the longitudinal deformation of the rolled pipe, but also plays a vital role in wall thickness control, surface quality, and even the production efficiency of the entire unit. Therefore, people are accustomed to calling the name of the tube rolling process the type of the unit, such as continuous tube rolling mill, automatic tube rolling mill, and precision tube rolling mill.
Due to the high requirements for the quality of seamless steel pipes and the efficient and rapid development of hot-rolled steel pipe units, the steel pipe finishing process and equipment are further developed and modernized. Walking cooling beds, multi-roller steel pipe straightening machines, high-efficiency pipe cutting machines and pipe saws, fast milling head chamfering machines, automatic length measuring, weighing, spray printing and mechanized strapping devices have emerged and are widely used. The development of related technologies, especially the maturity of the continuous casting round billet process and the application of on-line detection and automatic control technologies have further promoted the development of seamless steel pipe production technology. The higher quality requirements of the products and the special pipes require further heat treatment (normalizing, annealing, quenching and tempering, etc.) and machining (threading, peeling, polishing, end thickening, etc.).