The influence of heat treatment process on mold deformation
1. The influence of heating speed
Generally speaking, during quenching and heating, the faster the heating rate, the greater the thermal stress generated in the mold, which is likely to cause deformation and cracking of the mold. Especially for alloy steel and high-alloy steel, due to their poor thermal conductivity, special preheating is required. For some high-alloy molds with complex shapes, multiple preheating is required.
However, in individual cases, rapid heating can sometimes reduce deformation. At this time, only the surface of the mold is heated, while the center remains "cold", so the tissue stress and thermal stress are reduced accordingly, and the deformation resistance of the center is greater. , Thereby reducing the quenching deformation, according to some factory experience, it has a certain effect on solving the hole pitch deformation.
2. The influence of heating temperature
The quenching heating temperature affects the hardenability of the material, and at the same time affects the composition and grain size of austenite.
(1) From the perspective of hardenability, high heating temperature will increase the thermal stress, but at the same time increase the hardenability, so the structure stress will also increase and gradually dominate. For example, carbon tool steels T8, T10, T12, etc., when quenched at general quenching temperature, the inner diameter shows a tendency to shrink, but if the quenching temperature is increased to ≥850°C, the hardenability increases and the structural stress gradually accounts for Dominance, so the inner diameter may show a tendency to bulge.
(2) From the perspective of austenite composition, the increase in quenching temperature increases the austenite carbon content, and the squareness of martensite after quenching (increased specific volume), which increases the volume after quenching.
(3) From a closer look at the effect on the Ms point, the higher the quenching temperature, the coarser austenite grains, which will increase the deformation and cracking tendency of the parts.
In summary, for all steel grades, especially some high-carbon medium and high alloy steels, the quenching temperature will obviously affect the quenching deformation of the mold. Therefore, the correct selection of the quenching heating temperature is very important.
Generally speaking, choosing too high a quenching heating temperature is not good for deformation. Under the premise of not affecting the performance, a lower heating temperature is always used. However, for some steel grades with more retained austenite after quenching (such as Cr12MoV, etc.), the amount of retained austenite can also be adjusted by adjusting the heating temperature to adjust the deformation of the mold.
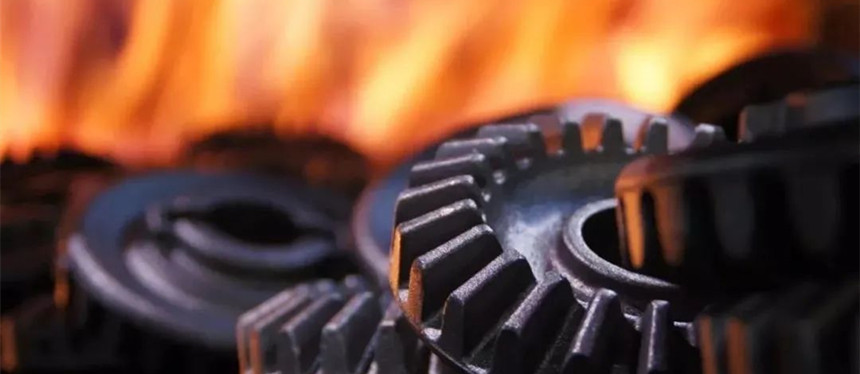
3. The influence of quenching cooling rate
In general, increasing the cooling rate above the Ms point will significantly increase the thermal stress, and as a result, the deformation caused by the thermal stress tends to increase; increasing the cooling rate below the Ms point will mainly increase the deformation caused by the tissue stress. Big.
For different steel grades, due to the different heights of the Ms points, when the same quenching medium is used, there are different deformation tendencies. For the same steel grade, if different quenching media are used, they also have different deformation tendencies due to their different cooling capabilities.
For example, the Ms point of carbon tool steel is relatively low, so when water cooling is used, the influence of thermal stress tends to prevail; while when cooling is used, the structural stress may prevail.
In actual production, molds are usually not fully quenched when they are graded or graded-austempered, so thermal stress is often the main effect, which tends to shrink the cavity. However, because the thermal stress is not very large at this time, Therefore, the total deformation is relatively small. If water-oil double-liquid quenching or oil quenching is used, the thermal stress caused is greater, and the cavity shrinkage will increase.
4. The influence of tempering temperature
The effect of tempering temperature on deformation is mainly caused by the transformation of the structure during the tempering process. If the phenomenon of "secondary quenching" occurs during the tempering process, the retained austenite is transformed into martensite, and the specific volume of the martensite generated is larger than that of the retained austenite, which will cause the mold cavity to expand; For some high-alloy tool steels, such as Cr12MoV, high temperature quenching is used to require red hardness as the main requirement. When multiple tempering, the volume expands once every time the tempering is performed.
If tempered in other temperature regions, the specific volume decreases due to the transformation of quenched martensite to tempered martensite (or tempered sorbite, tempered troostite, etc.), and therefore, the cavity tends to shrink.
In addition, during tempering, the relaxation of the residual stress in the mold also affects the deformation. After the mold is quenched, if the surface is in a state of tensile stress, the size will increase after tempering; on the contrary, if the surface is in a state of compressive stress, it will shrink. But of the two effects of organizational transformation and stress relaxation, the former is the main one.