Low temperature carbon steel welding
Low temperature carbon steel welding
What are the technical points of low temperature carbon steel welding?
Welding of low temperature steel
Usually the temperature range of -10 ~ -196 ℃ is called "low temperature" (counting from -40 ℃ in China), and it is called "ultra-low temperature" when it is lower than -196 ℃. Low temperature steel is a special steel developed rapidly to meet the needs of energy, petrochemical and other industrial sectors. Low temperature steel requires sufficient strength, plasticity and toughness under low temperature working conditions, and should have good processing properties, mainly used to manufacture welded structures that work at low temperatures of -20 ~ -253 ℃, such as storage and transportation of various liquefied gases Container etc.
1. Selection of welding method and heat input
Commonly used welding methods include electrode arc welding, submerged arc automatic welding, tungsten argon arc welding, and gas-shielded arc welding.
When welding low-alloy steel with low temperature, in order to avoid the formation of a coarse structure in the weld metal and the near-seam area and try not to swing, narrow bead, multi-layer multi-layer welding is used, the welding current should not be too large, and fast multi-pass welding should be used to reduce The weld bead is overheated, and the grains are refined by the reheating effect of multi-layer welding. In multi-pass welding, to control the temperature between passes, the welding should be performed with a small heat input, controlled below 20KJ / cm. If preheating is required, the preheating temperature and the interpass temperature during multi-layer multi-pass welding should be strictly controlled.
Welding line energy is also called welding heat input, which is the welding arc heat per unit length of weld.
Formula E = U • I / v (Joules / cm) where U: arc voltage (volts), I: welding current (ampere), and v: welding speed (cm / min).
Welding line energy is an important factor that affects the performance of the welding head. When the welding current and arc voltage increase, the welding line energy increases, and when the welding speed decreases, the welding line energy increases.
For low-temperature steel, the welding line energy is too large, the joint toughness decreases more seriously, so that the pressure vessel is prone to instantaneous damage when operating at low temperature. Therefore, when welding, we must strictly control the welding current, arc voltage, welding speed, to ensure the various performance indicators of the welded joint.
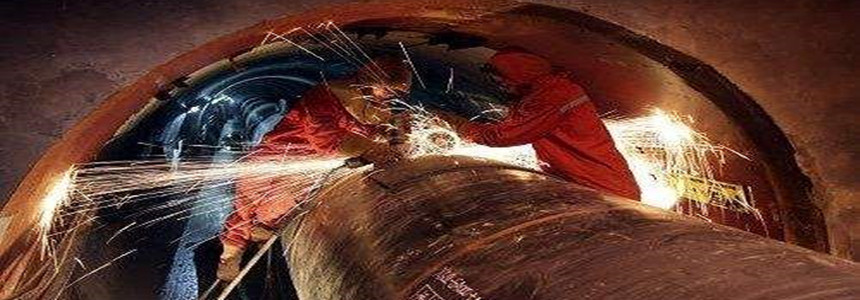
2. Welding characteristics and technological measures of low temperature steel
Low-temperature steel has a low carbon content, its hardening tendency and cold cracking tendency are small, and it has good weldability. However, excessive welding line energy will cause the formation of coarse-grained structure in the weld and heat-affected zone, which greatly reduces the low-temperature toughness. The sudden change of the structure and the strong pair in the manufacturing will cause high stress in the local area of the structure, which will increase The brittle failure of the equipment at low temperature. For this reason, the following should be done during the welding process:
(1) Adopt small welding line energy to minimize overheating and prevent the appearance of coarse structure on the welding joint. Electrode arc welding usually uses 12-15KJ / cm, submerged arc welding is usually 20KJ / cm. For this reason, the electrode arc welding should not use the φ5 electrode as much as possible. The submerged arc automatic welding mostly uses φ3.2 welding wire. The electrode arc welding is about 2mm per layer and the submerged arc automatic welding is about 2.5mm.
(2) Using straight weld bead, multiple fast pressure welding. The purpose is to reduce overheating and the latter weld bead has a tempering effect on the former weld bead to refine the grain.
(3) Avoid strong pairing, so that there is no stress concentration in the structure.
(4) As much as possible to reduce the interlayer temperature between the weld bead, avoid the weld bead at high temperature for a long time, try to achieve discontinuous welding.
(5) Usually use ultra-low hydrogen electrode and flux, so we must strictly follow the drying system for drying treatment before welding, the electrode used has not been used up for more than 4 hours, should be returned to the secondary store and re-dried before use. In addition, for low-temperature steel electrodes, the deposited metal diffusion hydrogen re-inspection should be carried out according to relevant standards before use. The mercury method is usually used, which is implemented according to GB / T3965-2012.
(6) In winter construction and thicker structure, it should be properly preheated, at least preheated to above 15 ℃. For the welding of large and thick plates, the preheating temperature is generally 50 ℃, and the temperature between the channels is controlled between 50 and 150 ℃.
(7) Arc starting shall use arc starting plate or arc starting in the groove, and shall not start at non-welded parts.
(8) The stress-relieving heat treatment after welding of low temperature steel can reduce the risk of brittle fracture of low alloy steel welding products.
Selection of common low temperature steel welding materials
16MnDR:
J507GR, J507RH,-E5015-G or E5016-G H10Mn2 SJ101-F5P4-H10Mn2
09MnNiDR:
W707Ni, W807Ni-E5515-N5 E7015-C1L, E7016-C1L F7P7-ENi2-Ni2
H07MnNDR SJ603W-F5P7-H07MnNiDR
08Ni3DR: For temperatures below -100 ° C, generally imported welding consumables E7015-C2L, E7016-C2L F7P15-ENi3-Ni3
SA-203 Gr.D is an ASME material and requires an impact of -101 ℃ E7016-C2L F7P15-ENi3-Ni3
Welding inspection of low temperature pressure vessel
1. Regulatory requirements: Welding joints on low-alloy steel low-temperature pressure vessels with a design temperature below -40 ° C are subject to 100% MT testing and qualified according to JB / T4730.4-2005 Class I.
2. If HG20584 is designed and implemented, for the welding of low-temperature steel materials that require ultrasonic testing, the groove surface and the groove surface after rooting should be 100% MT checked, and qualified according to JB / T4730.5-2005 level I.
3. The stress concentration caused by defects at low temperature will increase the tendency of the structure to break brittlely at low temperature. Care should be taken to avoid defects such as craters, under-penetration and poor weld formation. Under normal circumstances, the residual height of the weld should be minimized, and sometimes it is required to be smooth after welding; the corner joints should be rounded and not allowed to protrude outwards. Those with poor roundness or poor forming of the weld must be polished; side.
4. The surface of the cryogenic container shall not be marked with steel stamps.
What are the technical points of low temperature carbon steel welding?
Welding of low temperature steel
Usually the temperature range of -10 ~ -196 ℃ is called "low temperature" (counting from -40 ℃ in China), and it is called "ultra-low temperature" when it is lower than -196 ℃. Low temperature steel is a special steel developed rapidly to meet the needs of energy, petrochemical and other industrial sectors. Low temperature steel requires sufficient strength, plasticity and toughness under low temperature working conditions, and should have good processing properties, mainly used to manufacture welded structures that work at low temperatures of -20 ~ -253 ℃, such as storage and transportation of various liquefied gases Container etc.
1. Selection of welding method and heat input
Commonly used welding methods include electrode arc welding, submerged arc automatic welding, tungsten argon arc welding, and gas-shielded arc welding.
When welding low-alloy steel with low temperature, in order to avoid the formation of a coarse structure in the weld metal and the near-seam area and try not to swing, narrow bead, multi-layer multi-layer welding is used, the welding current should not be too large, and fast multi-pass welding should be used to reduce The weld bead is overheated, and the grains are refined by the reheating effect of multi-layer welding. In multi-pass welding, to control the temperature between passes, the welding should be performed with a small heat input, controlled below 20KJ / cm. If preheating is required, the preheating temperature and the interpass temperature during multi-layer multi-pass welding should be strictly controlled.
Welding line energy is also called welding heat input, which is the welding arc heat per unit length of weld.
Formula E = U • I / v (Joules / cm) where U: arc voltage (volts), I: welding current (ampere), and v: welding speed (cm / min).
Welding line energy is an important factor that affects the performance of the welding head. When the welding current and arc voltage increase, the welding line energy increases, and when the welding speed decreases, the welding line energy increases.
For low-temperature steel, the welding line energy is too large, the joint toughness decreases more seriously, so that the pressure vessel is prone to instantaneous damage when operating at low temperature. Therefore, when welding, we must strictly control the welding current, arc voltage, welding speed, to ensure the various performance indicators of the welded joint.
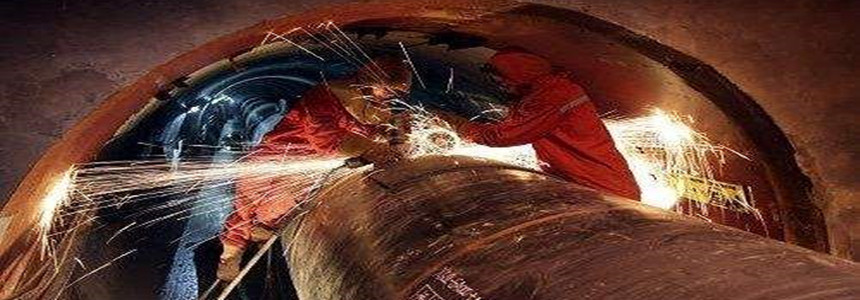
2. Welding characteristics and technological measures of low temperature steel
Low-temperature steel has a low carbon content, its hardening tendency and cold cracking tendency are small, and it has good weldability. However, excessive welding line energy will cause the formation of coarse-grained structure in the weld and heat-affected zone, which greatly reduces the low-temperature toughness. The sudden change of the structure and the strong pair in the manufacturing will cause high stress in the local area of the structure, which will increase The brittle failure of the equipment at low temperature. For this reason, the following should be done during the welding process:
(1) Adopt small welding line energy to minimize overheating and prevent the appearance of coarse structure on the welding joint. Electrode arc welding usually uses 12-15KJ / cm, submerged arc welding is usually 20KJ / cm. For this reason, the electrode arc welding should not use the φ5 electrode as much as possible. The submerged arc automatic welding mostly uses φ3.2 welding wire. The electrode arc welding is about 2mm per layer and the submerged arc automatic welding is about 2.5mm.
(2) Using straight weld bead, multiple fast pressure welding. The purpose is to reduce overheating and the latter weld bead has a tempering effect on the former weld bead to refine the grain.
(3) Avoid strong pairing, so that there is no stress concentration in the structure.
(4) As much as possible to reduce the interlayer temperature between the weld bead, avoid the weld bead at high temperature for a long time, try to achieve discontinuous welding.
(5) Usually use ultra-low hydrogen electrode and flux, so we must strictly follow the drying system for drying treatment before welding, the electrode used has not been used up for more than 4 hours, should be returned to the secondary store and re-dried before use. In addition, for low-temperature steel electrodes, the deposited metal diffusion hydrogen re-inspection should be carried out according to relevant standards before use. The mercury method is usually used, which is implemented according to GB / T3965-2012.
(6) In winter construction and thicker structure, it should be properly preheated, at least preheated to above 15 ℃. For the welding of large and thick plates, the preheating temperature is generally 50 ℃, and the temperature between the channels is controlled between 50 and 150 ℃.
(7) Arc starting shall use arc starting plate or arc starting in the groove, and shall not start at non-welded parts.
(8) The stress-relieving heat treatment after welding of low temperature steel can reduce the risk of brittle fracture of low alloy steel welding products.
Selection of common low temperature steel welding materials
16MnDR:
J507GR, J507RH,-E5015-G or E5016-G H10Mn2 SJ101-F5P4-H10Mn2
09MnNiDR:
W707Ni, W807Ni-E5515-N5 E7015-C1L, E7016-C1L F7P7-ENi2-Ni2
H07MnNDR SJ603W-F5P7-H07MnNiDR
08Ni3DR: For temperatures below -100 ° C, generally imported welding consumables E7015-C2L, E7016-C2L F7P15-ENi3-Ni3
SA-203 Gr.D is an ASME material and requires an impact of -101 ℃ E7016-C2L F7P15-ENi3-Ni3
Welding inspection of low temperature pressure vessel
1. Regulatory requirements: Welding joints on low-alloy steel low-temperature pressure vessels with a design temperature below -40 ° C are subject to 100% MT testing and qualified according to JB / T4730.4-2005 Class I.
2. If HG20584 is designed and implemented, for the welding of low-temperature steel materials that require ultrasonic testing, the groove surface and the groove surface after rooting should be 100% MT checked, and qualified according to JB / T4730.5-2005 level I.
3. The stress concentration caused by defects at low temperature will increase the tendency of the structure to break brittlely at low temperature. Care should be taken to avoid defects such as craters, under-penetration and poor weld formation. Under normal circumstances, the residual height of the weld should be minimized, and sometimes it is required to be smooth after welding; the corner joints should be rounded and not allowed to protrude outwards. Those with poor roundness or poor forming of the weld must be polished; side.
4. The surface of the cryogenic container shall not be marked with steel stamps.