Insulation elbow
Insulation elbow
The thermal insulation elbow is one of the thermal insulation pipe fittings. The thermal insulation elbow is composed of high-density polyethylene outer casing, polyurethane foam thermal insulation layer and inner working steel pipe.
Insulation elbows are mainly used for the turning of thermal insulation straight pipes. They are generally used in conjunction with thermal insulation pipes. They are used for compensation according to the design of thermal insulation pipelines, so that the elbows can also have sufficient thermal insulation performance. Degrees, 45 degrees, 60 degrees, 90 degrees.
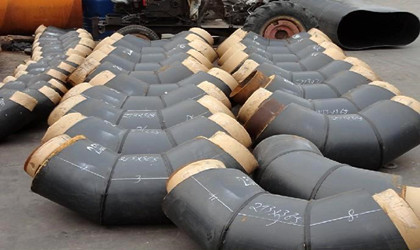
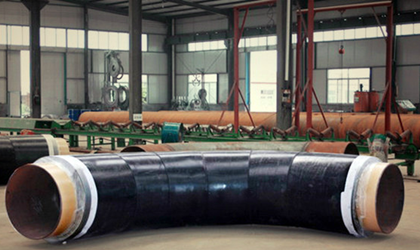
Standard for insulation elbow
CJ / T200—2004 "Technical Conditions for Preheated Directly Buried Steam Insulation Pipes for Urban Heating
CJ / T104 --- 2005 "Technical Specification for Urban Heating Directly Buried Steam Pipelines"
SY / T114-2000, SY / T115-2001 "High Density Polyethylene Polyurethane Foam Insulated Steel Pipe"
Material for insulation elbow
The materials of insulation elbow are generally as follows:
Carbon steel: ASTM / ASME A234 WPB, WPC
Alloy: ASTM / ASME A234 WP 1-WP 12-WP 11-WP 22-WP 5-WP 91-WP911, 15Mo3 15CrMoV, 35CrMoV
Stainless steel: ASTM / ASME A403 WP 304-304L-304H-304LN-304N ;ASTM / ASME A403 WP 316-316L-316H-316LN-316N-316Ti ;ASTM / ASME A403 WP 321-321H ASTM / ASME A403 WP 347-347H
Low temperature steel: ASTM / ASME A402 WPL3-WPL 6
High-performance steel: ASTM / ASME A860 WPHY 42-46-52-60-65-70
Cast steel, alloy steel, stainless steel, copper, aluminum alloy, plastic, argon leaching, PVC, PPR, RFPP (reinforced polypropylene), etc.
Application of insulation elbow
Insulation elbows are widely used in liquid and gas transportation pipeline networks, chemical pipeline insulation engineering petroleum, chemical industry, central heating heating network, central air conditioning ventilation pipelines, municipal engineering pipeline turns. Insulation pipes (including elbows, tees, and tees) are direct buried prefabricated insulation pipes with good insulation performance, safety and reliability, and low engineering cost. It effectively solves the problems of heat preservation, heat preservation, thermal insulation of elbows, sliding lubricating, waterproofing and anti-corrosion of exposed pipe ends and bending points in various pipeline projects such as heating, cooling, thermal power, electricity, and chemical engineering. It not only has the advanced technology and practical performance that traditional trenches and overhead laying pipelines are incomparable, but also has significant social and economic benefits, and the conversion of thermal insulation straight pipes.
The insulation elbow has the same principle as the directly buried insulation pipe. It is a new technology of waterproof, leakproof, impermeable, pressure resistant and fully enclosed embedding. It is a major breakthrough in the use of direct embedding technology in areas with high groundwater levels. . The primary problem of the protection pipe of the directly buried pipeline is the reliability of tight waterproofing. In addition, it must have good mechanical strength. Due to the high strength of the insulation elbow, the high-density polyethylene outer casing is closely combined with the polyurethane foam insulation layer and the inner working steel pipe to make it waterproof. The reliability of the sealing performance is very high. In addition, its high temperature resistance is also unmatched by other external protection tubes.
Advantages of insulation elbow
Structural mechanism of insulation elbow
1. High-density polyethylene anti-corrosion layer: high-density polyethylene pipe protects the elbow from corrosives and plants, and prolongs the service life of the pipe fittings Support the working pipe and be able to bear a certain external load to ensure that the working pipe works normally.
2. Polyurethane foam layer: high temperature resistance, medium temperature guarantee, normal temperature of the outer protective tube surface, and thermal insulation of the inner working tube to ensure that the foam is not carbonized
3. Working steel pipe: ensure that the conveying medium flows normally.
The rigid polyurethane foam material in the insulation elbow has a stable porosity structure and is basically closed-cell, so it not only has excellent insulation performance, but also good freeze-thaw resistance and sound absorption. The average life of the on-site mold-cast polyurethane rigid foam insulation structure can reach more than 30 years under the conditions of normal use and maintenance. All materials can be protected from damage caused by dry, wet or galvanic corrosion, insects, fungi or algae growth, or rodent damage, etc. under normal use conditions during the life of the structure. damage. All materials of this product are compatible with each other and meet the quality requirements of relevant national standards.
Since the birth of polyurethane synthetic materials in the 1930s, polyurethane foam insulation has been rapidly developed as an excellent thermal insulation material, and its application range is becoming more and more extensive. It is used in various pipelines such as heating, cooling, oil transportation, steam transportation, etc. Product main projects: petroleum gas pipeline engineering, natural gas pipeline engineering, chemical plants, power plants, shipyards, pharmaceuticals, dairy products, beer, beverages, water conservancy and other projects.