Improve the heat transfer coefficient of the heat exchanger
How to improve the heat transfer coefficient of heat exchanger
Change the flow of fluid
(1) Increase the flow rate
Increasing the flow rate can change the flow state and increase the degree of turbulence. For example, the splitting of the tube pass and the shell pass in the shell-and-tube heat exchanger is one of the measures to increase the flow rate, increase the process length and disturbance. Increasing the flow velocity in the tube during turbulent flow has a significant effect on enhancing heat transfer, but it must be noted that increasing the flow velocity is also restricted by various factors. Therefore, various factors should be weighed in the design or actual use, and the best flow rate or the flow rate allowed by the fluid conveying machine should be selected.
(2) Jet impact
This is a method in which the fluid is sprayed directly onto the solid surface through a circular or slit nozzle for cooling or heating. Since the fluid directly impacts the solid wall, the flow is short and the boundary layer is thin, so the convective heat transfer coefficient increases significantly. When the liquid jet is used to impact the heating surface, if the heat flux density is high enough to produce boiling, it becomes a two-phase jet impact heat exchange. Experiments show that not only can the boiling heat transfer coefficient be increased, but also the burnout point can be delayed, and the critical heat flow value can be significantly increased.
(3) Add insert
Various types of inserts such as metal wire, metal spiral ring, disk-shaped member, twisted iron, wing-shaped object, etc. are placed in the tube or outside the tube, which can enhance the disturbance, destroy the flow boundary layer and increase the heat transfer. For example, after a twisted iron spoiler twisted by thin metal strips is inserted into the tube, the fluid forms a strong swirling flow to enhance heat transfer. If it can be in close contact with the tube wall during insertion, it can still function as a fin and expand the heat transfer surface. A large number of experimental studies have shown that the addition of inserts can significantly enhance forced convection heat transfer, but it will also cause operational problems such as increased flow resistance, easy channel blockage and fouling. When using the insert, it should follow the entire process of the pipeline to maintain enhanced heat transfer in the entire process. Moreover, when choosing the form of the insert, consideration should be given to enhancing heat transfer with small resistance.
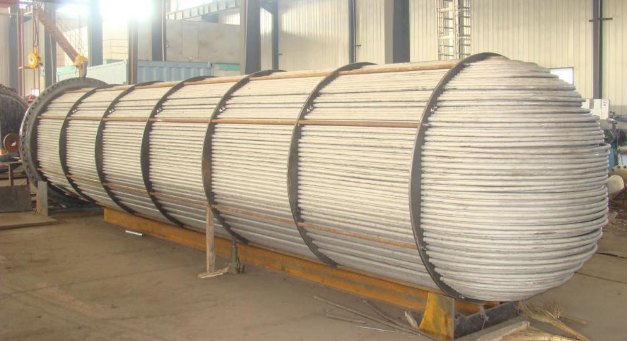
(4) Add rotating flow device
The centrifugal force of the rotating flow will cause the fluid to produce a secondary circulation, which will enhance heat transfer. Some of the above-mentioned inserts, such as twisted iron, metal spiral wire, etc., in addition to their own characteristics, can also produce rotational flow. Here are some elements or devices that specifically generate rotational flow. For example, a vortex generator, which can make the fluid enter the tube in a tangential direction under a certain pressure for violent rotation. Studies have shown that the degree of heat transfer enhancement by vortex is related to the Reynolds number. At a certain heat source temperature, the convective heat transfer coefficient increases with the Re value, and will reach a certain maximum value and then decrease. In application, the actual Re value should be controlled to be close to the critical Re value when the convective heat transfer coefficient is maximized, so as to make full use of the effect of rotating flow. In addition to fluid rotation, there are also cases where the heat transfer surface rotates. When the pipe rotates around a different axis, the secondary circulation generated by its centrifugal force, shear stress, gravity, and buoyancy can promote heat transfer enhancement. The effect of pipe rotation on the heat release of laminar flow is significant, but the effect is not obvious in turbulent flow. The experiments of subcooled boiling and large-space boiling have shown that the boiling heat transfer coefficient or critical heat load can be improved for pipes with spiral slopes and tangential groove vortex generators.
(5) Rely on external energy
There are basically three measures: ① Use mechanical or electrical methods to vibrate the heat transfer surface or the fluid, or stir the fluid to mix well. Experiments show that vibration has a certain effect on free flow heat transfer and forced flow heat transfer. The effect of boiling heat transfer is not obvious, but when the fluid is vibrating, boiling in a large space can significantly increase the critical heat load. This method has certain difficulties in the specific application of large heat exchange equipment. The use of mechanical transmission to drive the agitator, through the good mixing of fluids to enhance convective heat transfer, the effect is significant, so it is widely used, especially for fluids with high viscosity. ② Apply sound waves or ultrasonic waves to the fluid to make it alternately compressed and expanded to increase pulsation and enhance heat transfer. Based on the results of experiments conducted by various researchers, it is shown that for liquids or gases, the effect of acoustic waves is more obvious only when they are in laminar or transitional flow in the tube. The effect of heat transfer on bubbly boiling in large spaces is minimal, and the heat transfer improvement on transition boiling or film boiling is more significant. It has a certain effect on condensation heat transfer and free flow heat transfer. In the practical use of sound wave enhancement measures, attention should be paid to solving the problem of how to more effectively transmit acoustic vibration or ultrasonic vibration to the inside of the heat exchange equipment. ③Electromagnetic field action. Applying high voltage to the fluid participating in the heat exchange forms a non-uniform radial electric field. Such an electrostatic field can cause the mixing of the dielectric fluid near the heat transfer surface, thereby enhancing the convective heat transfer. Experiments show that the enhancement effects of free-flow heat transfer, film boiling heat transfer, and condensation heat transfer are all significant. If magnet powder is mixed into the fluid, the magnetic field can strengthen the heat transfer even at a large Re number. For example, mixing magnet powder in water or oil can increase the heat transfer coefficient by more than 50% under the action of a magnetic field.
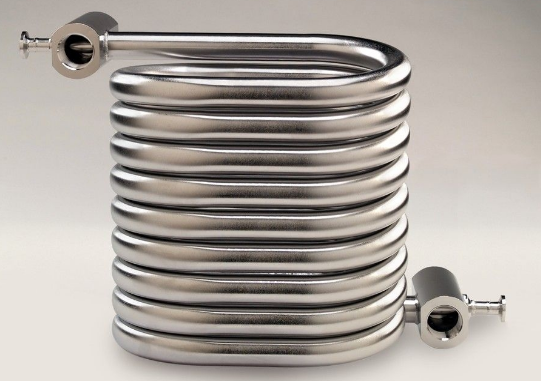
Change the physical properties of communicators
The physical properties of the fluid have a greater impact on the convective heat transfer coefficient. Generally, fluids with larger thermal conductivity and volumetric specific heat have a larger heat transfer coefficient. For example, the volume of water cooling in cooling equipment can be much smaller than that of air cooling, because the value of α between air and the wall is in the range of 1~60 W/(m2·℃), and the value of α between water and the wall is between 200 and 12000 W/(m2·℃) range. Another way to change certain properties of the fluid is to add some additives to the fluid. This is a new topic in the research of additive heat transfer enhancement that has been formed in the past two to three decades. The additive can be solid or liquid, and it is combined with the heat exchange fluid to form a gas-solid, liquid-solid, vapor-liquid, and liquid-liquid mixed flow system.
Change the heat exchange surface condition
The nature, shape, and size of the heat exchange surface have a great influence on the convective heat transfer coefficient. Usually, the following methods can be used to enhance heat transfer:
(1) Increase wall roughness
Increasing the wall surface roughness is not only conducive to forced flow heat exchange inside the tube, but also beneficial to boiling and condensation heat exchange and forced flow heat exchange outside the tube. The same roughness has different effects on heat transfer under different flow and heat transfer conditions. Increasing roughness will also increase the flow resistance, which should be considered in industrial applications.
(2) Change the shape and size of the heat exchange surface
In order to increase the convective heat transfer coefficient, various special-shaped tubes and surface grooves can also be used, such as elliptical tubes, spiral tubes, corrugated tubes, variable section tubes and longitudinal grooved tubes. The equivalent diameter of an elliptical tube is smaller than that of a round tube under the same cross-sectional area, so the heat transfer coefficient is large. In addition to the slightly increased heat transfer area of other special-shaped tubes, due to the change of the surface shape, the fluid will continuously change the direction and speed in the flow, which promotes the enhancement of turbulence and the thinning of the boundary layer thickness, which can enhance the heat transfer. For low-ribbed threaded pipes, it also has the effect of thinning the condensation film during condensation and heat exchange. It is very advantageous to use low-ribbed threaded pipes for the condensation of organic working fluids (freon, etc.). The micro-fin tube developed on the basis of the low-fin tube is more conducive to the condensation and heat exchange of low-boiling organic media such as freon, such as the C tube in Japan and the DAC tube in my country. For vertical condensation, if a longitudinally grooved tube is used, the surface tension of the liquid pulls the condensate at the peak into the trough, forming a very thin condensate film at the peak, and the trough drains the condensate, so the condensation heat transfer is enhanced.
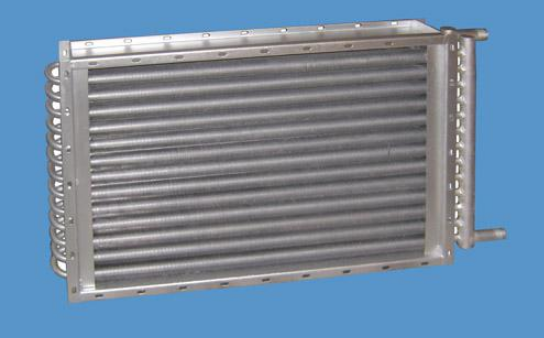
(3) Improve surface structure
Sintering, EDM processing or cutting the metal tube to form a very thin porous metal layer on the surface of the tube to form a porous tube, which can enhance boiling and condensation heat transfer. Such as: American high heat flux tube used for boiling heat exchange, Japanese E-tube, German T-tube, my country's DAE tube, etc. In addition, for example, in the boiling heat exchange liquid, a porous object is placed on the heating surface, and the steam is continuously removed through the porous heating surface, which is the so-called "inhalation" method, thus making the film boiling heat transfer Improved.
(4) Surface coating
During condensation heat exchange, a layer of material with low surface tension, such as polytetrafluoroethylene, can be coated on the heat exchange surface to cause bead condensation, which is beneficial to increase the heat transfer coefficient. For boiling heat transfer, according to the physical properties of the heated liquid, a film of a certain substance of appropriate thickness can be coated on the heating surface to make it a non-wetting surface, which can significantly increase the boiling heat transfer coefficient. In the use of solar energy, a thin layer of selective material is coated on the heat-absorbing surface of the collector to increase its absorption rate of sunlight and reduce its emissivity, so as to enhance the absorption of radiant heat and reduce the loss of radiant heat. purpose.