Duplex Stainless Steel Processing and Manufacturing (7)
Practical Guide for Processing and Manufacturing Duplex Stainless Steel (7)
The application of duplex stainless steel is increasing, and users are becoming more and more familiar with this type of stainless steel. This article focuses on one of the difficulties in the application of duplex stainless steel-machining and welding, introduces the various characteristics of duplex stainless steel, and gives the basic principles and practical information for processing and welding duplex stainless steel. The content includes: the history, chemical composition, metallurgy, corrosion resistance, mechanical properties, physical properties, technical conditions, quality control, cutting, forming, welding, application of duplex stainless steel.
The full text is longer and will be published in several parts, welcome to follow!
15 Application of duplex stainless steel
Flue gas desulfurization
According to air quality control plans around the world, coal-fired power facilities are facing an uncertain future. It is required to further reduce SO2 emissions, and flue gas desulfurization (FGD) is a method to achieve low SO2 emissions. The use of lime or limestone slurry to "wet scrub" SO2 in flue gas is a mature technology that has been used as a basic system in power station boiler systems since the 1970s.
Modern scrubbers can currently remove 90% of SO2 in the exhaust gas. A modern FGD unit consists of several zones with different temperatures, chloride content and pH. 2205 stainless steel (S32205) has been used in FGD devices in Europe, Asia and America because of its lower cost and better corrosion resistance compared with austenitic stainless steel. Because of its high strength, good corrosion resistance and high toughness after welding, it has become the most popular material for FGD absorption towers.
Desalination
Due to its high chloride content and high-temperature corrosive process environment, seawater desalination has made the material withstand the most stringent test. The history of desalination is basically the history of material development, because customers in the desalination industry need to find a balance between meeting the requirements of corrosion resistance and keeping investment within an acceptable range. In the early desalination projects, the evaporators of the multi-stage flash (MSF) and multi-effect (MED) desalination equipment were made of carbon steel. Later, MSF evaporators were generally covered with 316L austenitic stainless steel. The MED evaporation chamber was first coated with epoxy resin and then covered with stainless steel.
The advantage of using duplex stainless steel is its high strength (twice that of traditional austenitic steel) combined with high corrosion resistance. Therefore, the duplex stainless steel evaporator can be made of thinner steel plate and requires less materials and welding. More benefits include easier handling and less comprehensive environmental impact.
A breakthrough in the concept of duplex stainless steel In 2003, 2205 duplex stainless steel was used to manufacture solid duplex steel evaporators, installed in Melittah MSF equipment and Zuara MED equipment in Libya. In 2004, a facility with a daily production capacity of 4 million gallons (MIGD) was put into production.
The next stage of duplex stainless steel used in seawater desalination was in early 2004. Two different types of duplex stainless steel were used in the structure of the evaporator-high corrosion resistance 2205 was used to make parts used in the harshest conditions. 2304 makes parts that are used under not too harsh conditions.
Later, the concept of combining 2205 and UNS S32101 was used to build three sets of MSF equipment: Taweelah B (Abu Dhabi, 69.2 MIGD), Jebel Ali L2 (Dubai, 55 MIGD) and Abu Fontas B2 (Qatar, 30 MIGD). Since 2003, the combination of 2304 and 2205 duplex stainless steels has been used to build the world's largest MED equipment-Al Hidd in Bahrain, with a capacity of 60 MIGD.
Petroleum and natural gas
In the oil and gas industry, duplex steel has played a vital role in helping to withstand harsh conditions. This is not only because of its corrosion resistance and mechanical properties, but also because its pitting and crevice corrosion resistance is better than standard austenitic alloys, and its pitting equivalent value (PREN) is usually higher than 40.
Duplex stainless steel is mainly used in fluid pipes, process pipeline systems and equipment, such as separation devices, washing devices and pumps. Under the sea, these materials are used in downhole production pipelines, pipe fittings and manifolds, Christmas tree parts, fluid pipes, and pipelines that transport corrosive oil and gas. Super duplex stainless steel (25% Cr), due to its effective resistance to design stress, is often used in the following areas: round bars, forgings, castings, thin plates, thick plates, pipes, fasteners, etc. Super duplex steel also has excellent fatigue resistance and good galvanic compatibility with other high alloy stainless steels.
Umbilical cables are used for wellhead operation control using hydraulic lines, and can also be used for chemical injection. Since the introduction of steel umbilical cables to the market, duplex stainless steel has been the most commonly used material. In recent years, the trend of developing deep-sea oil and gas fields requires longer umbilical cables. Increasing the strength of the material can reduce the weight of the umbilical cable and make the length longer. The current development trend is to use the umbilical cable in warm water and introduce the riser into the umbilical cable. Therefore, the requirements for corrosion resistance and mechanical strength have increased. A new type of super duplex stainless steel with better corrosion resistance and higher strength than super duplex stainless steel has been developed for umbilical cables.
Biofuels
On land, the biofuel industry (especially ethanol) is a growing field of duplex steel applications. 2205 stainless steel has been used in Singapore's NExBTL process equipment for biofuel production. In a large-scale biofuel project in the Port of Amsterdam, the Dutch tank manufacturer Oostwouder Tank-& Silobouw BV selected S32101 for the tank group manufactured by Noba Vetveredeling BV. In the expansion project of the Agroetanol ethanol plant on Händelö Island in Sweden, S32101 was also designated for the manufacture of vessels and pipelines. In many ethanol plant applications, economical duplex steel has been used to replace 300 series austenitic stainless steel.
Food and drinks
Economical duplex steels have also proven their value in the food and beverage industry. This material was used in two projects in Spain, a food storage and a wine storage. In the Port of Barcelona, Emypro SA uses S32101 to build food storage tanks instead of 304/304L. In Daimiel, southern Spain, the wine storage warehouse built by the Spanish tank manufacturer Martinez Sole for Garcia Carrion used duplex stainless steel S32101 and 2304 instead of 304/316L for the first time for the construction of all storage tanks. The top cover and the uppermost top plate.
Construction industry
Dual-phase steel continues to play an important role in the construction of bridges. The bridges are in corrosive and salty conditions and require high load-bearing strength. The Stonecutters Bridge in Hong Kong and the Double Helix Pedestrian Bridge in Singapore both use 2205 duplex stainless steel. In 2006, Stonecutters Bridge used 2,000 tons of 2205 dual-phase steel plates and pipes, and the surface part was built with custom-sized plates by Chinese manufacturers. The plate is polished and shot blasted to have the best reflectivity during the day and night.
The double helix pedestrian bridge uses 570 tons of duplex stainless steel. The stunning design of this bridge contains two spiral stainless steel tubes similar to the DNA structure. The double helix and its supporting structure use 2205 duplex steel tubes and plates respectively. The stainless steel surface provides evening lighting by reflecting light, which is used to enhance the design effect.
The world's largest stainless steel roof at the new Doha International Airport in Qatar was constructed using molybdenum-containing economic duplex stainless steel S32003. The most prominent feature of the terminal building is its undulating roof, which is said to be the largest stainless steel roof in the world. The roof area is about 195,000 square meters, and about 1,600 tons of duplex stainless steel is used. Several factors must be considered when choosing stainless steel grades, the most important of which is the distance from the airport to the sea. The roof must not only withstand the high temperature and humidity of the Middle East, but also withstand salt corrosion. The choice of duplex stainless steel materials not only meets the performance requirements, but also has cost advantages and a good strength-to-weight ratio.
The application of duplex stainless steel is increasing, and users are becoming more and more familiar with this type of stainless steel. This article focuses on one of the difficulties in the application of duplex stainless steel-machining and welding, introduces the various characteristics of duplex stainless steel, and gives the basic principles and practical information for processing and welding duplex stainless steel. The content includes: the history, chemical composition, metallurgy, corrosion resistance, mechanical properties, physical properties, technical conditions, quality control, cutting, forming, welding, application of duplex stainless steel.
The full text is longer and will be published in several parts, welcome to follow!
(Continued from the previous article)
15 Application of duplex stainless steel
Flue gas desulfurization
According to air quality control plans around the world, coal-fired power facilities are facing an uncertain future. It is required to further reduce SO2 emissions, and flue gas desulfurization (FGD) is a method to achieve low SO2 emissions. The use of lime or limestone slurry to "wet scrub" SO2 in flue gas is a mature technology that has been used as a basic system in power station boiler systems since the 1970s.
Modern scrubbers can currently remove 90% of SO2 in the exhaust gas. A modern FGD unit consists of several zones with different temperatures, chloride content and pH. 2205 stainless steel (S32205) has been used in FGD devices in Europe, Asia and America because of its lower cost and better corrosion resistance compared with austenitic stainless steel. Because of its high strength, good corrosion resistance and high toughness after welding, it has become the most popular material for FGD absorption towers.
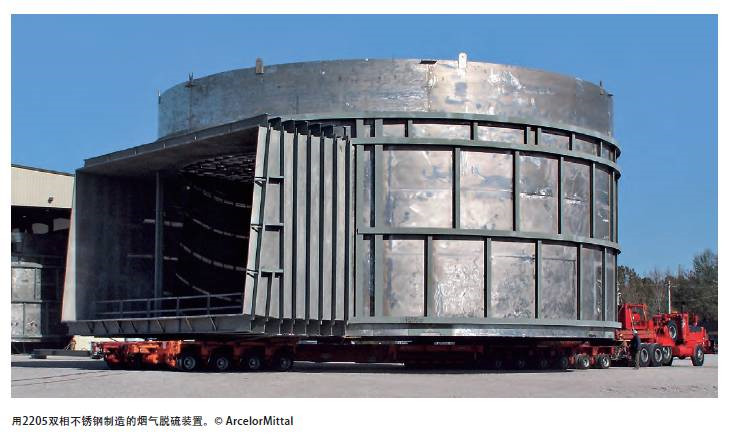
Desalination
Due to its high chloride content and high-temperature corrosive process environment, seawater desalination has made the material withstand the most stringent test. The history of desalination is basically the history of material development, because customers in the desalination industry need to find a balance between meeting the requirements of corrosion resistance and keeping investment within an acceptable range. In the early desalination projects, the evaporators of the multi-stage flash (MSF) and multi-effect (MED) desalination equipment were made of carbon steel. Later, MSF evaporators were generally covered with 316L austenitic stainless steel. The MED evaporation chamber was first coated with epoxy resin and then covered with stainless steel.
The advantage of using duplex stainless steel is its high strength (twice that of traditional austenitic steel) combined with high corrosion resistance. Therefore, the duplex stainless steel evaporator can be made of thinner steel plate and requires less materials and welding. More benefits include easier handling and less comprehensive environmental impact.
A breakthrough in the concept of duplex stainless steel In 2003, 2205 duplex stainless steel was used to manufacture solid duplex steel evaporators, installed in Melittah MSF equipment and Zuara MED equipment in Libya. In 2004, a facility with a daily production capacity of 4 million gallons (MIGD) was put into production.
The next stage of duplex stainless steel used in seawater desalination was in early 2004. Two different types of duplex stainless steel were used in the structure of the evaporator-high corrosion resistance 2205 was used to make parts used in the harshest conditions. 2304 makes parts that are used under not too harsh conditions.
Later, the concept of combining 2205 and UNS S32101 was used to build three sets of MSF equipment: Taweelah B (Abu Dhabi, 69.2 MIGD), Jebel Ali L2 (Dubai, 55 MIGD) and Abu Fontas B2 (Qatar, 30 MIGD). Since 2003, the combination of 2304 and 2205 duplex stainless steels has been used to build the world's largest MED equipment-Al Hidd in Bahrain, with a capacity of 60 MIGD.
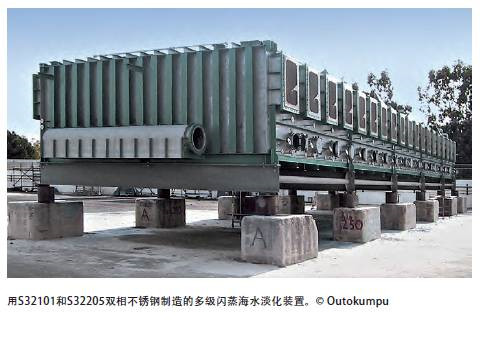
Petroleum and natural gas
In the oil and gas industry, duplex steel has played a vital role in helping to withstand harsh conditions. This is not only because of its corrosion resistance and mechanical properties, but also because its pitting and crevice corrosion resistance is better than standard austenitic alloys, and its pitting equivalent value (PREN) is usually higher than 40.
Duplex stainless steel is mainly used in fluid pipes, process pipeline systems and equipment, such as separation devices, washing devices and pumps. Under the sea, these materials are used in downhole production pipelines, pipe fittings and manifolds, Christmas tree parts, fluid pipes, and pipelines that transport corrosive oil and gas. Super duplex stainless steel (25% Cr), due to its effective resistance to design stress, is often used in the following areas: round bars, forgings, castings, thin plates, thick plates, pipes, fasteners, etc. Super duplex steel also has excellent fatigue resistance and good galvanic compatibility with other high alloy stainless steels.
Umbilical cables are used for wellhead operation control using hydraulic lines, and can also be used for chemical injection. Since the introduction of steel umbilical cables to the market, duplex stainless steel has been the most commonly used material. In recent years, the trend of developing deep-sea oil and gas fields requires longer umbilical cables. Increasing the strength of the material can reduce the weight of the umbilical cable and make the length longer. The current development trend is to use the umbilical cable in warm water and introduce the riser into the umbilical cable. Therefore, the requirements for corrosion resistance and mechanical strength have increased. A new type of super duplex stainless steel with better corrosion resistance and higher strength than super duplex stainless steel has been developed for umbilical cables.
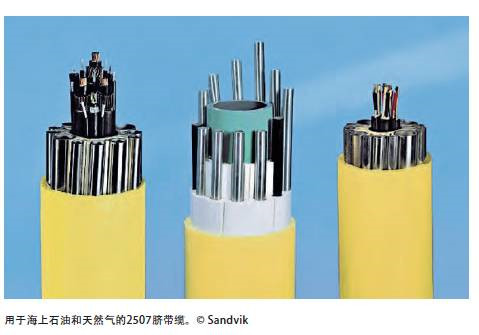
Biofuels
On land, the biofuel industry (especially ethanol) is a growing field of duplex steel applications. 2205 stainless steel has been used in Singapore's NExBTL process equipment for biofuel production. In a large-scale biofuel project in the Port of Amsterdam, the Dutch tank manufacturer Oostwouder Tank-& Silobouw BV selected S32101 for the tank group manufactured by Noba Vetveredeling BV. In the expansion project of the Agroetanol ethanol plant on Händelö Island in Sweden, S32101 was also designated for the manufacture of vessels and pipelines. In many ethanol plant applications, economical duplex steel has been used to replace 300 series austenitic stainless steel.
Food and drinks
Economical duplex steels have also proven their value in the food and beverage industry. This material was used in two projects in Spain, a food storage and a wine storage. In the Port of Barcelona, Emypro SA uses S32101 to build food storage tanks instead of 304/304L. In Daimiel, southern Spain, the wine storage warehouse built by the Spanish tank manufacturer Martinez Sole for Garcia Carrion used duplex stainless steel S32101 and 2304 instead of 304/316L for the first time for the construction of all storage tanks. The top cover and the uppermost top plate.
Construction industry
Dual-phase steel continues to play an important role in the construction of bridges. The bridges are in corrosive and salty conditions and require high load-bearing strength. The Stonecutters Bridge in Hong Kong and the Double Helix Pedestrian Bridge in Singapore both use 2205 duplex stainless steel. In 2006, Stonecutters Bridge used 2,000 tons of 2205 dual-phase steel plates and pipes, and the surface part was built with custom-sized plates by Chinese manufacturers. The plate is polished and shot blasted to have the best reflectivity during the day and night.
The double helix pedestrian bridge uses 570 tons of duplex stainless steel. The stunning design of this bridge contains two spiral stainless steel tubes similar to the DNA structure. The double helix and its supporting structure use 2205 duplex steel tubes and plates respectively. The stainless steel surface provides evening lighting by reflecting light, which is used to enhance the design effect.
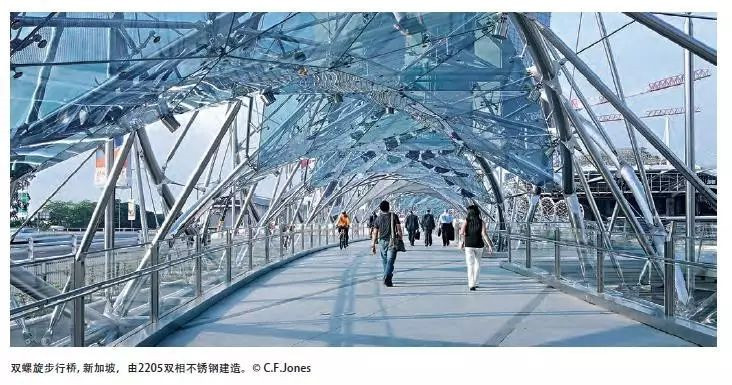
The world's largest stainless steel roof at the new Doha International Airport in Qatar was constructed using molybdenum-containing economic duplex stainless steel S32003. The most prominent feature of the terminal building is its undulating roof, which is said to be the largest stainless steel roof in the world. The roof area is about 195,000 square meters, and about 1,600 tons of duplex stainless steel is used. Several factors must be considered when choosing stainless steel grades, the most important of which is the distance from the airport to the sea. The roof must not only withstand the high temperature and humidity of the Middle East, but also withstand salt corrosion. The choice of duplex stainless steel materials not only meets the performance requirements, but also has cost advantages and a good strength-to-weight ratio.
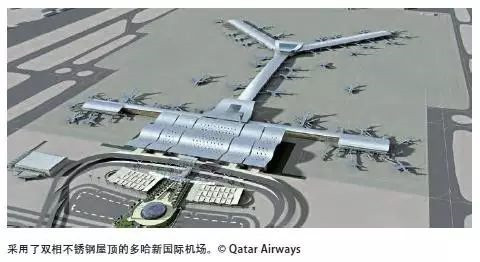
(End of full text)