Duplex Stainless Steel Processing and Manufacturing (5)
Practical Guide for Duplex Stainless Steel Processing and Manufacturing (5)
The application of duplex stainless steel is becoming more and more extensive, and users are more and more familiar with such stainless steel. This article focuses on one of the difficulties of duplex stainless steel application-processing and welding, introduces the various characteristics of duplex stainless steel, and gives the basic principles and practical information for processing and welding duplex stainless steel.
Contents include: history, chemical composition, metallurgy, corrosion resistance, mechanical properties, physical properties, technical conditions, quality control, cutting, forming, welding, and applications of duplex stainless steel.
The full text is longer and will be published in several parts. Welcome to pay attention!
(Continued from the previous article)
12 Welding of duplex stainless steel
12.1 General welding guidelines
12.1.1 The difference between duplex stainless steel and austenitic stainless steel
The welding problem of austenitic stainless steels is often related to the weld metal itself, especially the tendency of hot cracks generated during the solidification of welds where all austenite or austenite is dominant. For general austenitic stainless steel, adjusting the composition of the filler metal to make it have more ferrite content can minimize these problems. High-alloy austenitic stainless steel requires the use of nickel-based filler metals. Austenitic solidification is inevitable and can be controlled by reducing heat input and multi-pass welding.
Due to the high content of ferrite in duplex stainless steel, it has very good resistance to thermal cracking, and thermal cracking is rarely considered when welding. The main problem of duplex stainless steel welding is related to the heat affected zone, not the weld metal. The problem with the heat affected zone is loss of corrosion resistance and toughness or cracking after welding. In order to avoid the above problems, the focus of the welding process is to minimize the total residence time in the "red heat" temperature range, rather than controlling the heat input of any welding. Experience shows that this method can optimize the welding process from a technical and economic perspective.
According to the above introduction, some general guidelines for duplex stainless steel welding will be given, as well as the application of these basic knowledge and guidelines in specific welding methods.
12.1.2 Selection of original materials
The adaptability of duplex stainless steel to welding can vary significantly with changes in chemical composition and production process. The importance of the parent material containing sufficient nitrogen has been repeatedly emphasized. If the original material is slowly cooled through the 700-1000°C temperature range, or allowed to air-cool through this range for one minute before water quenching, then the time that should have been left to the welder to complete the welding without any harmful phase precipitation is exhausted. The important point is that the material actually processed and manufactured, its composition and metallurgical conditions of the production process should be the same as the quality conditions of the material used for welding process qualification. The end-user technical conditions and quality control chapter (Chapter 6) gives a method for selecting the original material based on the composition and appropriate test specifications.
12.1.3 Cleaning before welding
The requirement to clean all heated parts before welding is applicable not only to duplex stainless steels, but also to all stainless steels. Determine the chemical composition of the base metal and filler metal without additional pollution sources. Dust, grease, grease, paint, and any form of moisture can interfere with the welding operation and adversely affect the corrosion resistance and mechanical properties of the weldment. If the material is not thoroughly cleaned before welding, no matter what the process qualification is, it is invalid.
12.1.4 Joint design
The design of duplex stainless steel welded joints must help to fully penetrate and avoid the presence of unfused base metal in the solidified weld metal. It is better to use cutting rather than grinding wheel to grind the groove to make the thickness or gap of the welding zone uniform. When grinding is necessary, special attention should be paid to the uniformity of the groove processing and its cooperation. In order to ensure complete fusion and penetration, any grinding burrs should be removed. For austenitic stainless steels, experienced welders can overcome certain defects in groove processing by controlling the welding torch. However, for duplex stainless steels, these techniques will cause the material to stay in the harmful temperature range longer than expected, resulting in results that exceed the requirements of the qualified process.
Some joint designs of duplex stainless steel are shown in Figure 17. Other designs are reasonable if they can ensure that the weld is fully penetrated and the risk of burn-through is minimal.
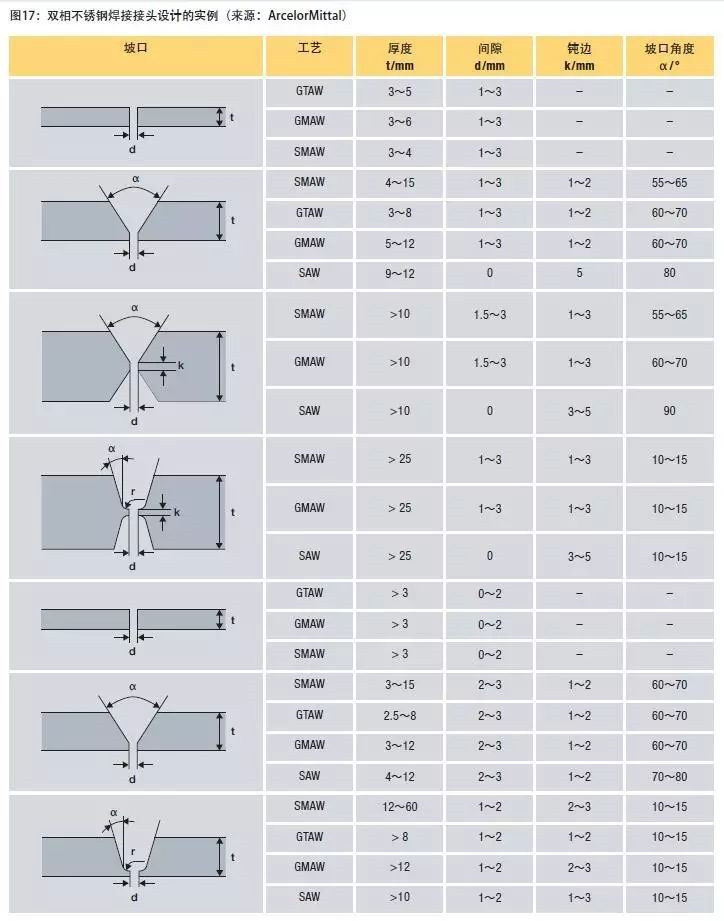
12.1.5 Warm-up
Since preheating can be harmful, preheating is generally not recommended. If there is no special justification, preheating should not be used as a process. Preheating may be beneficial if used to eliminate moisture formed by cold weather or condensation at night. When preheating to remove moisture, the steel should be evenly heated to about 100°C and should be cleaned after cleaning the groove.
12.1.6 Heat input and interlayer temperature
Duplex stainless steel can tolerate relatively high heat input. After solidification of the weld metal, the thermal crack resistance of the two-phase structure is much better than that of the austenitic weld metal. Duplex stainless steel has a higher thermal conductivity and a lower coefficient of thermal expansion, and the welds do not have as high local thermal stress as austenitic stainless steel. Hot cracking is not a common problem.
The extremely low heat input can lead to excessively high ferrite content in the fusion zone and heat-affected zone of the base metal, and reduced toughness and corrosion resistance. The extremely high heat input increases the risk of forming intermetallic phases. To prevent problems in the heat-affected zone, the welding procedure specification should allow rapid cooling of the zone after welding. The temperature of the workpiece is important because it has the greatest effect on the cooling of the heat affected zone. The maximum interlayer temperature of economical and standard duplex stainless steel is generally limited to 150℃, and super duplex stainless steel is limited to 100℃. This limit value should be used for welding procedure qualification, and production welding should also be monitored to ensure that the interlayer temperature is not higher than the temperature used during procedure qualification. Electronic temperature sensors and thermocouples are good means to monitor the temperature between layers. In the welding procedure evaluation, it is best not to let the interlayer temperature of the multi-pass welding test piece be lower than the interlayer temperature that can be achieved in actual manufacturing. When performing a large amount of welding, the cost-effective way is to plan the welding process so that there is sufficient cooling time between passes.
12.1.7 Post-weld heat treatment
Duplex stainless steels do not require post-weld stress relief treatment, and this may be harmful because heat treatment can precipitate intermetallic phases or α'(475°C) brittle phases, reducing toughness and corrosion resistance. Post-weld heat treatment temperature exceeding 315℃ will adversely affect the toughness and corrosion resistance of duplex stainless steel.
The post-weld heat treatment of duplex stainless steel should include complete solution annealing, followed by water quenching (see Table 10). After solution welding, complete solution annealing should be considered, because if no over-alloyed filler metal is used in the welding process, the ferrite content in the microstructure will be very high.
If complete solution annealing and quenching are performed after welding, such as the manufacture of parts, heat treatment should be considered as part of the welding process. Annealing can solve the problem of excessive ferrite and intermetallic phases. The manufacturing process allows some undesirable intermediate states before the finished product is annealed.
12.1.8 Ideal phase balance
It is generally considered that the phase balance of duplex stainless steel is "50-50", with equal amounts of austenite and ferrite. However, strictly speaking, this is not correct, because modern duplex stainless steel contains 40% to 50% ferrite, and the rest is austenite. It is generally believed that when duplex stainless steel contains at least 25% ferrite and the rest is austenite, the unique performance advantages of duplex stainless steel can be obtained.
In some welding methods, especially those based on flux protection, the phase balance has been adjusted toward the higher austenite content to improve toughness and compensate for the loss of toughness caused by the increased oxygen content of the weld by the flux. The toughness of these filler metals is far lower than the high toughness value that can be achieved after the solution treatment of the steel plate or steel pipe, but the toughness of the weld metal is still sufficient to meet the expected requirements. No welding method can make the toughness of the weld metal as good as the toughness achieved after the rolled material is fully annealed. If the ferrite content of the weld metal is controlled to be greater than the minimum value required for the annealing treatment of duplex stainless steel in the rolling mill, it will cause unnecessary restrictions on the available welding methods.
The phase balance of the heat-affected zone, that is, the original forged steel plate or steel tube plus additional welding heat cycle, the ferrite content is usually slightly higher than the original material. It is almost impossible to accurately determine the phase equilibrium of the heat affected zone by metallography. If the ferrite content in this area is high, it may indicate that there has been an abnormal situation of excessive rapid cooling, which leads to excessive ferrite content and reduced toughness.
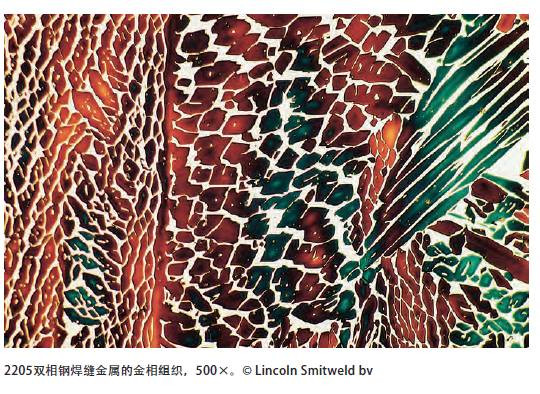
12.1.9 Welding of dissimilar metals
Duplex stainless steel can be welded with other duplex stainless steel, austenitic stainless steel, carbon steel and low alloy steel.
When the duplex stainless steel is welded with other duplex stainless steels, the duplex metal filler metal whose nickel content is higher than that of the base material is usually used. The high nickel content of the filler metal can ensure that the weld form a sufficient amount of austenite during the cooling process.
When welding duplex stainless steel and austenitic stainless steel, austenite stainless steel filler metal with low carbon and molybdenum content is often used; AWS E 309LMo/ER309LMo is usually used. The welding of duplex stainless steel with carbon steel and low alloy steel generally uses the same filler metal or AWS E309L/ER 309L. If nickel-based filler metals are used, they should not contain niobium. Since the strength of austenitic stainless steel is lower than that of duplex stainless steel, the welded joint using austenite stainless steel filler metal is not as strong as the duplex stainless steel base material.
Table 15 summarizes the commonly used filler metals when welding duplex stainless steels and dissimilar metals. These examples give the AWS electrode grade (E), but depending on the welding process, the shape of the joint and other conditions, welding wire (AWS grade ER) and flux cored wire may be used.
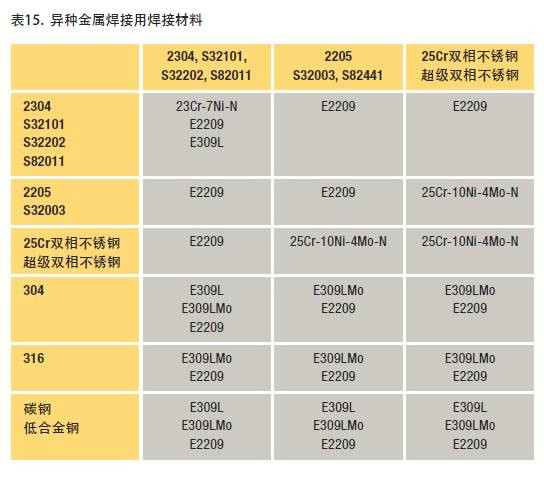
12.2 Welding process qualification
For standard austenitic stainless steels, the welding procedure qualification test is quite simple. Only a certain number of tests are carried out to prove that the materials, welding consumables and welding methods are qualified. These evaluation tests include hardness test and bending test (checking martensite and hot crack respectively), reflecting the problems that may occur when using ferritic, martensitic or austenitic stainless steel for a long time. Duplex stainless steels have no difficulty in meeting these requirements, but these tests cannot find intermetallic phases or excessive ferrite that may occur in duplex stainless steels. At the same time, due to the need to limit the total time within the temperature range of the heat affected zone, the performance of the duplex stainless steel will be sensitive to the thickness of the rolled material and the details of the actual welding operation. Therefore, "assessment" must be considered in a broad sense, that is, to prove that the welding process to be used in the manufacturing process will not lead to unacceptable loss of engineering performance, especially toughness and corrosion resistance.
It is safer to conduct welding procedure evaluation for each thickness and shape of welding, because the slight difference in the scheme may vary greatly in the actual manufacturing results. However, the complexity of the actual processing makes such tests very costly. Therefore, the most demanding welding conditions (determined by the material thickness, filler metal and welding method) of duplex stainless steel can achieve the purpose of saving and simplifying.
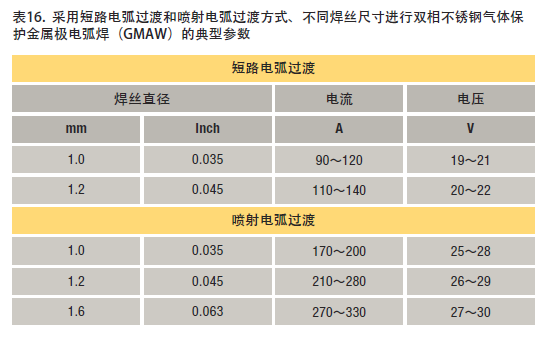
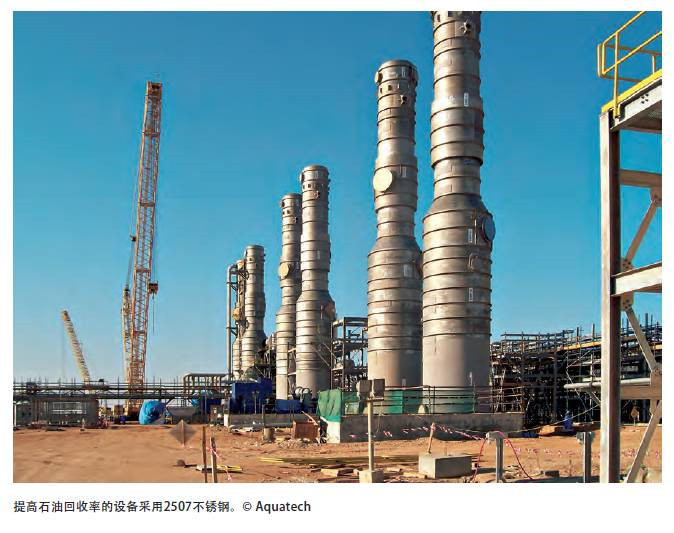
12.3 Welding method
Since the early 1980s, the commercialization of the second-generation duplex stainless steel has made great progress. Because of the limited understanding of the role of nitrogen in controlling the stabilization of phases, early views focused on limiting heat input. Due to strict control of heat input, many more economical welding methods with higher deposition rates, such as submerged arc welding, are considered unsuitable for duplex stainless steels. However, the performance of duplex stainless steel is very satisfactory, so many efforts have been made to adopt a more economical process. As a result, except for oxyacetylene welding due to carbon contamination of the associated weld, almost all welding processes are now available for duplex stainless steels.
12.3.1 Gas shielded tungsten arc welding (GTAW/TIG)
Gas-shielded tungsten arc welding (GTAW) is sometimes called inert gas-shielded tungsten (TIG) welding, and is especially suitable for short-pass manual welding. It can be operated automatically for simple geometries, but it is generally uneconomical as the main method of large-scale welding of large equipment. Because many processes still require some GTA welding even if another process is used as the main welding method, it is usually appropriate to evaluate the GTAW process for repairs and local repairs.
equipment
GTAW preferably uses a constant current power supply and uses high-frequency circuits to assist arc starting. GTA welding should use DC positive polarity (DCSP), and the electrode should be negative. The use of DC reverse polarity (DCRP) can damage the electrodes.
The electrode should be 2% thorium tungsten (AWS specification 5.12 EWTh-2 category). It helps to control the arc by grinding the electrode into a cone with an apex angle of 30 to 60 degrees and a cone facet. The ideal apex angle required for GTAW automatic welding to ensure penetration should be determined by tests in actual production.
Filler metal
Most of the filler metals used for duplex stainless steel welding are "matched", but the nickel content is generally higher (over-alloyed) compared to the matched forged products. The nickel content is usually about 2% to 4% higher than that of forged products. The nitrogen content in the filler metal is generally slightly lower than the base metal. It is generally believed that higher alloyed duplex stainless steel filler metals are suitable for welding low alloyed duplex stainless steels. Satisfactory results can be obtained by welding duplex stainless steel with austenitic stainless steel or carbon steel and alloy steel with "matching" filler metals.
protection
Like all gas shielded welding processes, when using GTAW, the weld pool must be protected from air oxidation and pollution. Inert gas, argon, dry welding grade argon with a purity of 99.95% or higher is most commonly used for this protection.
It is important that the gas treatment system is clean, dry, and leak-free, that the flow rate can be adjusted to supply a sufficient amount of gas, and that turbulence of protective gas and inhalation of air are prevented. The gas should be started a few seconds before starting the arc, and then kept for a few seconds after the arc is extinguished. The holding time is preferably long enough to cool the weld and heat affected zone below the oxidation temperature range of stainless steel. To protect the electrode, the recommended flow rate is 12 to 18 liters/minute when using a conventional gas diffusion screen (gas sieve). When using a conventional nozzle, the flow rate is required to be half of the above flow rate.
The flow rate of protective gas (also pure argon) on the back of the weld depends on the volume of the root of the weld, but it should be sufficient to ensure that the air is completely exhausted and the weld is fully protected (subject to no tempering color). Since argon is heavier than air, it should be fed from bottom to top. The amount of argon to be purged is at least 7 times the volume of the root of the weld.
With pure argon protection, satisfactory welding results can be obtained, but there is also the possibility of further improvement. Adding up to 3% dry nitrogen helps to retain the nitrogen content of the weld metal, especially for higher alloyed duplex stainless steels. However, it was found that the addition of nitrogen increased electrode consumption, and the addition of helium could partially offset this effect.
Avoid adding oxygen and carbon dioxide to the shielding gas, because they will reduce the corrosion resistance of the weld. Since the ferrite phase in duplex stainless steel may produce hydrogen embrittlement or hydrogen-induced cracking, hydrogen gas should not be used in the shielding gas and the shielding gas for the back of the weld.
If the torch is equipped with a gas delivery system and a water cooling system, they should be regularly inspected to ensure that the stored gas is dry and clean.
Technology and parameters
For duplex stainless steels, the uniformity of bevel, alignment, root blunt edges and gap preparation is particularly important. Although austenitic stainless steel allows the use of some welding techniques to overcome the defects of bevel preparation, the use of these techniques makes duplex stainless steels have a risk of prolonged residence time in the corresponding temperature range. If possible, copper backing is not recommended because duplex stainless steel is sensitive to surface contamination caused by copper.
Starting the arc outside the welding zone will produce local self-fusion welding joints, and the cooling rate is very fast, resulting in a decrease in local high ferrite content and corrosion resistance. In order to avoid this kind of problem, an arc should be started on the welded joint.
Full gas shielding should be used for tack welding. Tack welding should not be performed at the starting point of the root pass. Ideally, in order to avoid cracking of the root bead caused by tack welding, it is best to use intermittent welding and wear off the tack weld, or to locally grind the tack weld before welding the root.
The width of the root gap should be carefully maintained to ensure consistent heat input and dilution of the root bead. The start and end points of the root bead should be ground before welding to fill the bead. Between each welding pass, the workpiece should be allowed to cool to below 150°C (for standard duplex stainless steel) and below 100°C (for super duplex stainless steel) in order to allow sufficient time for cooling the heat-affected zone during subsequent welding.
The most commonly used filler metal for welding duplex stainless steels with the GTAW method is a "matching" filler metal with slightly nickel alloyed. Matching filler metals for higher alloyed duplex stainless steels, such as super duplex stainless steel filler metals, have been successfully used to weld 2205 base metals. The diameter of welding wire generally used is 1.6, 2.4 and 3.2 mm. The welding wire should be clean and dry, and should be kept in a covered container before use. The welding effect is best in the flat welding position. The welding torch should be kept as close to vertical as possible to minimize the amount of air inhaled into the shielding gas.
In order to meet various material thicknesses and joint design requirements, the flexibility of selecting heat input is great. The heat input calculated according to the following formula is generally in the range of 0.5~2.5kJ/mm.
Heat input (kJ/mm) = (V×A)/(S×1000)
Where V = voltage (volts)
A = current (ampere)
S = moving speed (mm/s) or
Heat input (kJ/inch)=(V×A×6)/(S×100)
Where V = voltage (volts)
A = current (ampere)
S = moving speed (in/min)
Generally recommended heat input:
2304 or economic duplex stainless steel 0.5~2.0 kJ/mm
2205 0.5~2.5 kJ/mm
2507 0.3~1.5 kJ/mm
With GTAW welding, if there is good gas protection and the residence time at certain temperatures is properly controlled, the welded seam has good toughness and corrosion resistance. GTAW is suitable for welding in various occasions. GTAW is often used to supplement and complete the final welding of large components assembled by other welding methods. It is very important to evaluate the welding process for various situations where GTAW may be used.
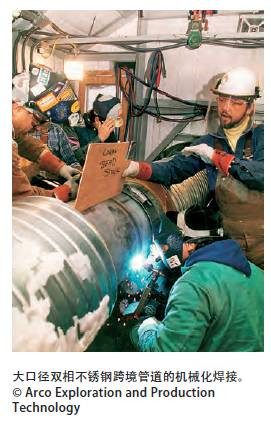
12.3.2 Gas shielded metal electrode arc welding (GMAW/MIG)
GMAW is sometimes referred to as inert gas metal arc welding (MIG), which is particularly suitable for welding long welds that require economical deposition of large amounts of weld metal. Automatic welding can be performed on the structure with simple shape. GMAW is often used for long bead welding, and then supplemented with GTAW for optimal control in complex operations.
equipment
GMAW requires special equipment, including constant voltage power supply with adjustable current up and down and voltage control or the ability to generate pulsed arc current. GMAW should use DC reverse polarity (DCRP) and the electrode should be positive. GMAW can have three arc transition methods.
Short circuit transition
This method requires separate control of inclination and secondary inductance, and is suitable for welding materials up to about 3 mm thick.
This method minimizes the heat input of GMAW and is especially suitable for thin gauge rolled materials that have a risk of deformation when higher heat input is used. It can also be used for welding in irregular positions.
Pulsed arc transition
This method requires two power supplies to provide two levels of output power, and pulses are provided by the power conversion. The metal transition amount is large in the jet transition phase, while the metal transition amount is small in the granular droplet transition phase. This combination has the advantage of high metal deposition speed but limited heat input.
Jet transition
In this way, the welding speed is high, the arc is stable, but the heat input is high. Generally limited to flat welding. It is economical to use this method to weld long and straight welds with medium-sized welds.
Filler metal
The consumable electrode used by GMAW is a continuous welding wire, which is supplied by an automatic feeding system through a welding torch. The filler metal used to weld duplex stainless steel with the GMAW method is a “matching” component with high nickel content (over alloying) to achieve the desired phase balance and performance in the welded state.
protection
The choice of GMAW shielding gas is slightly more complicated than GTAW, and depends to a large extent on whether the metal processing plant depends on the purchased mixed gas or has on-site mixed gas capability. The protective gas of GMAW ranges from pure argon to 80% argon and helium, nitrogen and oxygen are added. These gases are added to improve the weldability and finished product performance of welded components. The airflow speed depends on the transition mode, transition speed and welding wire diameter, but for welding wire with a diameter of 1 to 1.6 mm, the airflow speed is generally 12 to 16 l/min. During the welding process, the wire should not be over-extended to keep it in a gas-shielded state. Like GTAW, an intact gas delivery system is critical, and measures should be taken to prevent the protective gas from inhaling air. Since welding with a long bead is performed, it is important to start the gas protection from the ventilation device in order to ensure the welding quality. The shielding gas or the shielding gas on the back of the weld should not use hydrogen gas, because the ferrite phase in duplex stainless steel may produce hydrogen embrittlement or hydrogen-induced cracking.
Technology and parameters
Table 16 summarizes typical welding parameters for short-circuit arc transition and jet arc transition.
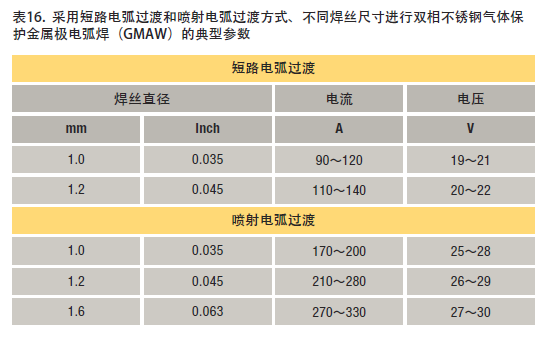
Just like GTAW welded duplex stainless steel, GMAW requires good and consistent groove machining, alignment, and blunt root edges or gaps. If possible, copper pads should be avoided because duplex stainless steels are sensitive to surface contamination caused by copper, and copper pads can cause excessive cooling in some cases.
Starting the arc outside the welding zone will produce local welding spots of self-fusion welding, and its cooling rate is very fast, resulting in the loss of local high ferrite content and corrosion resistance. In order to avoid problems, the welding joint should start arc. The method of fine grinding should be used to remove the arc starting point outside the weld area.
All gas welding should be used for tack welding. Tack welding should not be performed at the starting point of the root pass. In order to avoid cracking of the root weld bead caused by tack welding, it is best to use intermittent welding and wear away the tack weld, or to locally grind the tack weld before welding the root. The width of the root gap should be carefully maintained to ensure consistent heat input and dilution of the root bead. The start and end of the root bead should be ground before welding the filler metal. The workpiece should be allowed to cool to below 150°C between passes to allow sufficient time for the heat-affected zone of the subsequent weld pass to cool.
The diameter of welding wire generally used is 1.6, 2.4 and 3.2 mm. The welding wire should be clean and dry, and should be kept in a covered container before use. The catheter should be kept clean and dry. The welding effect is best in the flat welding position. The welding torch should be kept as close to vertical as possible to minimize the amount of air drawn into the shielding gas.
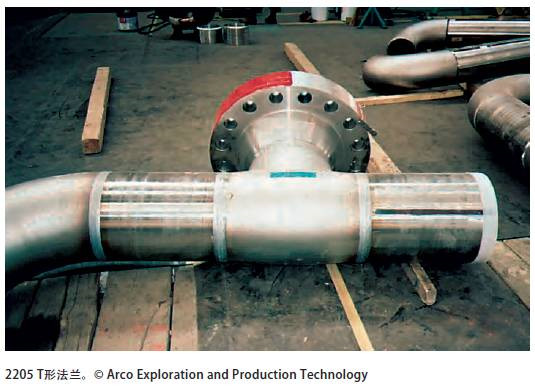
12.3.3 Flux-cored wire arc welding (FCW)
Flux-cored wire arc welding is one of the latest industrial developments of duplex stainless steel welding. Its successful application just shows how far-reaching and rapid the development of duplex stainless steel technology. The FCW method uses the same equipment as GMAW, and automatically supplies the flux-filled welding wire through the welding torch. The powder in the welding wire provides alloy elements and welding slag of part of the weld metal, protects the weld from air oxidation and pollution, and supplements the protective gas provided by the welding torch to protect the heat-affected zone. FCW is an economical welding method because of its high deposition rate. It is suitable for welding of irregular positions and materials of various thicknesses.
equipment
The equipment used to implement flux-cored wire arc welding is the same as that used by GMAW.
Filler metal
Due to the slightly lower weld toughness of the welding method using flux (this may be caused by the increase in the oxygen content of the weld metal), the nickel content of the filler metal of the FCW should be higher to make the austenite in the weld metal The content is higher than the nearly balanced base metal structure. Because the production of flux composition and FCW welding wire are patented, the FCW filler materials produced by different suppliers may be very different. When FCW is used for productive welding, the welding wire from the same source used in welding procedure evaluation should be used to avoid unstable production.
protection
The most commonly used shielding gases for FCW method for flat welding and vertical welding are 80% argon-20% carbon dioxide and 100% carbon dioxide, respectively. The flow rate of each shielding gas or welding method is 20-25l/min. It is important to control the extension length of the welding wire to suppress carbon increase, especially when 100% CO2 is used.
Process parameters
For welding wires with a diameter of 1.2mm, the typical current and voltage settings for flat welding and vertical welding are 150-200A, 22-38V and 60-110A, 20-24V, respectively. In addition, the recommendations for FCW welding techniques are the same as GMAW.
12.3.4 Manual arc welding (SMAW/electrode)
Manual arc welding, sometimes referred to as electrode or flux-coated electrode arc welding, is a very versatile method for welding complex shaped components in situations where location or protection is relatively difficult. Although the overall structure, especially the welding of smaller and more complex shapes that are relatively difficult to position or protect, can rely on the SMAW process, the most common situation is that SMAW and more competitive welding methods are used in conjunction with large-scale structures.
equipment
The equipment required for SMAW is a constant current power supply. SMAW uses direct current reverse polarity (DCRP) and the electrode is positive.
Filler metal
The SMAW electrode consists of a molten electrode with a coating. The coating may or may not contain additional alloying elements brought into the weld. The drug skin is a complex hybrid patented product, which can stabilize the arc, protect the metal during the arc transition, and protect the weld from contact with air during and after solidification. Due to the patented nature of the drug skin, the names are similar but products from different suppliers may vary greatly. The outstanding role of the coating is to improve the toughness or physical appearance of the weld. It can be specially designed for specific positions such as flat welding, irregular positions, and vertical welding to obtain optimal performance.
The coating of SMAW electrode is easy to absorb water, and the presence of water will greatly reduce their performance. The electrode should be kept in the factory sealed box before use. Once the package is opened, the electrode should be stored in an oven heated above 95°C to prevent moisture accumulation from causing pores or cracks in the weld. Since the coating increases the oxygen content of the weld, thereby reducing the toughness, the austenite content in the general SMAW electrode should be close to the maximum value, so that the weld metal will still have a good effect of the two-phase structure. The toughness of the weld is much lower than that of the base material, but it is usually much higher than the required toughness value of carbon steel and alloy steel. One error that sometimes appears in SMAW welding procedure qualification is that the ASTM A 923 test was used but the acceptance criteria were not adjusted appropriately. A low SMAW weld toughness value does not indicate the presence of intermetallic phases, but is due to the protection of oxygen in the coating. If the weld metal is required to reach a minimum impact value of 54J/40 ft·lb at -40°C/°F in accordance with the requirements for the base metal, this general welding method that has been used for many years and has achieved good results will be judged qualified. According to ASTM A 923, the minimum impact energy of the weld metal is 34J/25 ft·lb, and the minimum impact energy of the heat-affected zone is 54J/40 ft·lb.
protection
For SMAW, protection is usually not a problem, because this welding method relies on the gas protection generated by flux and electrode coating.
Technology and parameters
As shown in Table 17, the welding process parameters of SMAW are basically a function of the diameter of the electrode.
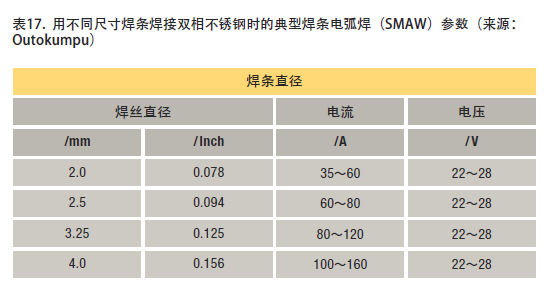
In order to maximize the protective effect of the flux, the welder should keep the arc as short as possible. If the gap is too wide, it is called "long arc", which may lead to weld pores, excessive oxidation, excessive heat input and reduced mechanical properties.
The weld bead at the root of the weld should use a small-sized electrode, and the filler bead should use a larger-sized electrode. The arc should always start in the weld zone. Any other arcing points or splashes should be removed by fine grinding.
Duplex stainless steel with a thickness of less than 2 mm should not be welded with SMAW. If possible, the workpiece should be as flat as possible, but the SMAW electrode can be used for welding in almost any position. The electrode should be at a 20° angle (inclination angle) to the workpiece. The electrode holder should be tilted forward in the direction of welding movement. Weld metal should be deposited using a straight narrow bead with the smallest amount of yaw. The current is set to stabilize the arc, and the weld and base metal melt well.
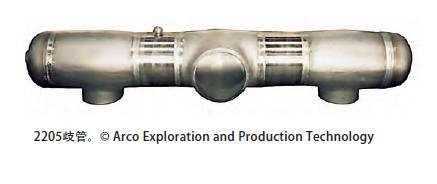
12.3.5 Submerged arc welding (SAW)
Submerged arc welding can be used to deposit large welds. Compared with the welding method with multiple passes and small deposits per pass, it has a shorter total residence time in the temperature range of the heat affected zone. Due to the solidification of the ferrite phase and the transformation of the duplex structure in the weld metal, duplex stainless steels can be welded with SAW and the risk of thermal cracking is minimal. However, in order to make the weld fully penetrated, it is necessary to adjust the joint design and welding parameters relative to austenitic stainless steel. If the SAW operation moves very fast and the groove is not designed properly, it will cause a crack in the centerline of the weld, and reducing the welding speed generally solves the crack problem. For the welding of large components and large straight weld passes, SAW is a cost-effective and effective method for welding duplex stainless steels. SAW is commonly used for processing thick-walled duplex stainless steel pipes.
Filling metal and protection
The usual duplex stainless steel matching filler metal is suitable for SAW. However, it is important to choose the flux correctly to obtain the desired performance. According to reports, using high alkalinity flux, duplex stainless steel has the best impact toughness.
Technology and parameters
Table 18 summarizes the typical parameters of duplex stainless steel SAW.
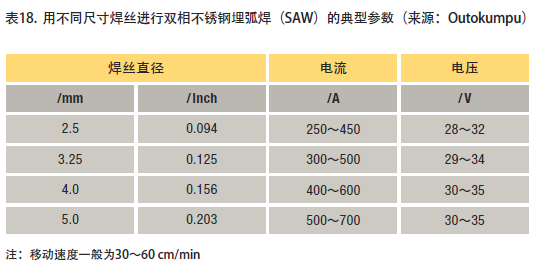
12.3.6 Electron beam welding and laser welding
The application experience of these welding methods on duplex stainless steel is positive. Using these welding processes, a very narrow heat-affected zone and rapid cooling can be obtained, and the formation of intermetallic phases can be avoided. However, high cooling rates can cause excessive ferrite formation in the weld, so when these welding methods are used, welding procedure qualification is critical. The solution annealing after welding can reduce the ferrite content and improve the ratio of austenite/ferrite phase in the weld.
12.3.7 Resistance welding
When single pulse resistance welding is used for spot welding, the heat affected zone cools quickly. This quenching of duplex stainless steel is even faster than austenitic stainless steel because duplex stainless steel has a higher thermal conductivity. In this case, the temperature of a thin layer of material immediately adjacent to the fusion line will reach the temperature range where the two-phase structure is completely transformed into ferrite. Cooling so fast, even duplex stainless steels with higher nitrogen content cannot form austenite in this temperature range, so the possible result is that the base metal has better toughness, and the weld has a continuous layer of ferrite in the middle Layers and poor toughness.
Programmable resistance welding machine can provide double pulse welding cycle, which is enough to reduce the cooling rate and prevent the continuous ferrite layer. Similarly, it is necessary to perform welding procedure qualification on materials of different thicknesses.
Resistance seam welding machines are less likely to cause similar problems, and the exposure time cannot be long enough to form intermetallic phases, but special attention should be paid to the possibility of excessive ferrite formation in the welding process evaluation.
(To be continued)