Duplex Stainless Steel Processing and Manufacturing (4)
Practical guide for duplex stainless steel manufacturing (4)
The application of duplex stainless steel is becoming more and more extensive, and users are more and more familiar with such stainless steel. This article focuses on one of the difficulties of duplex stainless steel application-processing and welding, introduces the various characteristics of duplex stainless steel, and gives the basic principles and practical information for processing and welding duplex stainless steel.
Contents include: history, chemical composition, metallurgy, corrosion resistance, mechanical properties, physical properties, technical conditions, quality control, cutting, forming, welding, and applications of duplex stainless steel.
The full text is longer and will be published in several parts. Welcome to pay attention!
(Continued from the previous article)
9 Cutting
The process usually used for austenitic stainless steel and carbon steel can be used for the cutting of duplex stainless steel, but some adjustments to the parameters are necessary to adapt to the different mechanical and thermal properties.
9.1 Sawing
Duplex stainless steel is more difficult to cut than carbon steel because of its high strength, high work hardening rate, and lack of inclusions that actually act as chip breakers. Adopt high-power machines, high-strength saw blade straightening system, coarse sawtooth saw blades, slow-to-medium cutting speeds, heavy feed, fully flowing coolant (preferably both lubricating and cooling Synthetic emulsifier so that the saw blade transfers the coolant to the workpiece) etc. for the best results. The cutting speed and feed rate should be similar to those of 316 austenitic stainless steel.
9.2 Cut
Duplex stainless steel is cut using the same equipment as 304 and 316 stainless steel, and generally does not require special adjustment. However, due to the high shear strength of duplex stainless steel, it is necessary to increase the shear power or reduce the shear thickness.
For hot-rolled and cold-rolled sheets, the shear strength of stainless steel is about 58% of the ultimate tensile strength. Duplex stainless steel behaves like a thicker 316 stainless steel, depending on their actual shear strength ratio. Therefore, the maximum thickness of 2304 and 2205 duplex stainless steels that can be sheared in a single shear is about 85% of the thickness of 304 and 316 stainless steels, and the maximum thickness of super duplex stainless steels that can be sheared in a single shear The thickness is 65% of ordinary austenitic stainless steel.
9.3 Slitting
The traditional steel coil slitter can be used to cut duplex stainless steel coils and steel strips. The duplex stainless steel coil is sent out from the decoiler, passes through the circular slitting blades of the upper and lower knife holders on the longitudinal cutting line, and the reel rewinds the cut steel coil. The position of the slitting blade can be adjusted according to the desired width of the coiled product. Because the strength of duplex stainless steel is higher than that of austenitic stainless steel, slitting tool wear and edge stability are more difficult to control. Tool steel or cemented carbide blades are required to maintain the good slitting edge quality of duplex stainless steel coils.
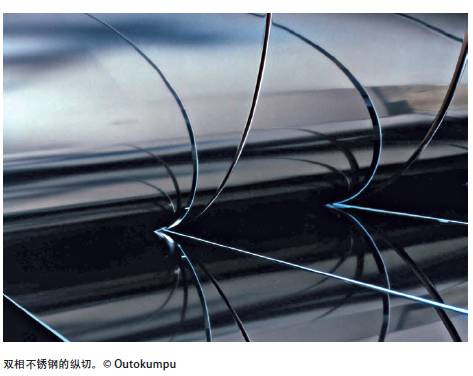
9.4 Punching
Punching can be seen as a difficult form of shearing. The high strength, rapid work hardening and tear resistance make duplex stainless steel relatively difficult to punch and wear tools. Operational experience in this area is limited, but duplex stainless steels behave like austenitic stainless steels that are twice as thick as duplex stainless steels. This index provides a good starting point for punching operations. High-alloyed duplex stainless steels with higher nitrogen content are more difficult to punch.
9.5 Plasma and laser cutting
Duplex stainless steel is generally processed by the same plasma cutting and laser cutting equipment as austenitic stainless steel. The slightly higher thermal conductivity and lower sulfur content of duplex stainless steel may have a slight effect on the optimal parameters, but no special adjustments are required to obtain acceptable results. The heat-affected zone of the plasma cutting process is generally very narrow, about 0.25 mm. This is because each cut is performed quickly, and then the middle or thin plate is quickly cooled. Usually the machining of the welding groove and the melting of the base metal near the weld zone during the welding process can remove the heat-affected zone of plasma cutting.
10 Forming
10.1 Thermoforming
Duplex stainless steels generally exhibit excellent hot formability, with relatively low forming loads at temperatures up to at least 1230°C. However, if the temperature of hot forming is too low, the deformation will gather in the weaker and less plastic ferrite, resulting in the ferrite cracking in the deformation zone. In addition, when the hot working temperature is lowered too much, a large amount of σ phase will be precipitated.
Most processors recommend that the maximum thermoforming temperature range be between 1100 and 1150°C. The reason why the upper temperature limit is recommended is due to the effect of high temperature on the dimensional stability of the workpiece and the tendency of scale to increase with increasing temperature. At high temperatures, the duplex stainless steel will become soft, and the processed workpieces such as container heads or pipes will bend or dent if not supported in the furnace. At these temperatures the steel will also become too soft due to some hot forming operations. Table 9 summarizes the hot forming temperature range and minimum soaking temperature of several duplex stainless steels. It is not necessary to start hot working from the highest temperature in this range. However, the steel must reach at least the lowest soaking temperature before hot working, and the furnace should be preheated to avoid slow heating through the temperature range where the σ phase is formed.
The uniformity of the temperature is important for the successful hot forming of duplex stainless steel. If the shape of the workpiece is irregular, the edge may be much cooler than the body, and these colder areas are at risk of cracking. To avoid cracking, when there is a danger that the temperature is lower than the minimum processing temperature in the local area, the workpiece needs to be reheated. Only when the temperature of the workpiece, especially the edge or thinner part, remains uniform, the lower limit of the thermoforming temperature range can be slightly expanded.
For sections with thicker sections, it is necessary to consider whether the water quenching speed is sufficient to prevent the precipitation of intermetallic phases. For forged and rolled 2205 duplex steel plates, the thickness of the plate is limited to about 150 to 200 mm. For forged and rolled super duplex stainless steel plates, the thickness is limited to 75 to 125 mm. The exact limit value depends on the composition of the duplex stainless steel and the quenching device The efficiency varies. For simple cylindrical workpieces, the diameter is limited to about 375 mm. If the inner diameter of the finished part is completely penetrated, perforating or machining the opening before the final heat treatment will greatly improve the cooling condition of the workpiece after the final annealing.
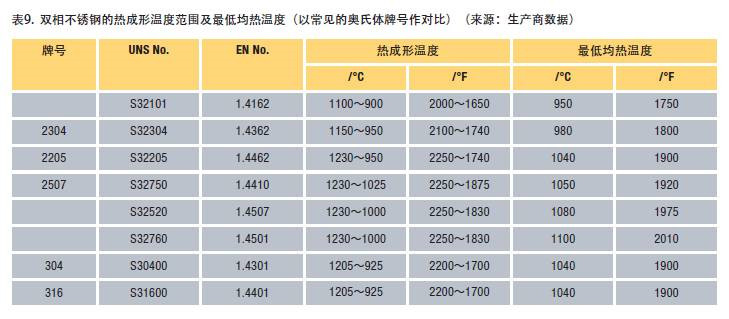
10.1.1 Solution annealing
After hot forming, complete solution annealing is required, followed by rapid quenching to fully restore the mechanical properties and corrosion resistance. The workpiece should be heated above the minimum solution annealing temperature, and then maintained for a long enough time to completely dissolve the intermetallic phase. A prudent principle is that the holding time should be comparable to the time the workpiece stays in the range of 650-980°C after complete annealing. Workpieces should be water quenched from the solution treatment temperature. When transferring to the quenching site after the final annealing, it is not allowed to stay in the temperature range of 700 ~ 1000 ℃ for a few minutes. Table 10 summarizes the minimum solution treatment temperature of duplex stainless steel.
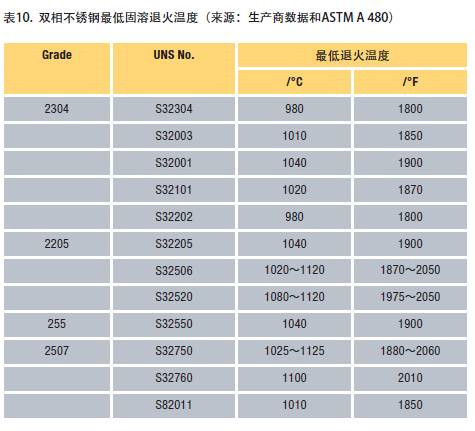
Duplex stainless steel is very soft at the solution annealing temperature. If the workpiece does not have sufficient support, it may twist and deform, which is a big problem for pipe products, especially large-diameter thin-walled pipes. Due to the high strength of duplex stainless steel at room temperature, the twisted duplex stainless steel products are more difficult to shape or straighten than austenitic stainless steel. Reduce the deformation by shortening the annealing time, slowing the heating to the solution temperature range or using a solution temperature lower than the recommended value, but it may not dissolve the intermetallic phase or cause the formation of more intermetallic phases, reducing the resistance Corrosiveness and toughness.
It is not advisable to use stress relief to reduce the cold working stress of forming or straightening operations. Duplex stainless steel itself has good resistance to chloride stress corrosion cracking, and reducing residual cold working stress only improves this performance to a certain extent. Below the solution treatment temperature, there is no such an appropriate temperature, and stress relief treatment can be performed at this temperature without forming an intermetallic phase that reduces corrosion resistance and toughness.
10.2 Warm forming
Sometimes a gentle heating method can be used to assist the forming operation of the workpiece. However, if the duplex stainless steel is heated above 315℃ for a long time, the embrittlement at 475℃ (see Figure 5) will lead to a decrease in room temperature toughness and corrosion resistance. At higher temperatures, there is a risk that the precipitation of intermetallic phases will be faster and more harmful. . Since these phases do not interfere with the forming process, the duplex stainless steel can be used for warm forming operations. When the processing temperature exceeds 300°C, complete solution annealing and rapid quenching should be performed after warm forming (see Table 10).
10.3 Cold forming
Duplex stainless steel shows good formability in various processing and manufacturing. Most duplex stainless steel applications require relatively simple forming, such as rolling of cylindrical sections, stamping forming, stamping or rolling forming of container and can heads. In these applications, a major concern is the high strength of duplex stainless steel and the power of forming equipment. The general estimate is that the forming of duplex stainless steels is similar to that of 300 series austenitic stainless steels that are twice as thick. The comparison of the minimum external forces required for several stainless steels to start plastic deformation during bending is shown in Figure 14. Using duplex stainless steel may make the thickness thin, but the amount of thinning will be less than the value expected from the increase in yield strength.
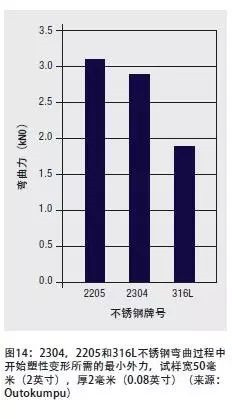
Even if the power of the equipment is high enough, there must be a margin for the higher rebound caused by the high strength of the duplex stainless steel (see Figure 12).
It must also be considered that the duplex stainless steel has lower plasticity than austenitic stainless steel. Most technical specifications require a minimum elongation of 15%-30% for duplex stainless steels, and a minimum 40% elongation for austenitic stainless steels. Although the actual elongation may be larger, the relationship between the two minimum values is appropriate and can be used as a useful guide for cold working operations. Compared with austenitic stainless steels, duplex stainless steels require a larger bending radius, and because of their lower plasticity, intermediate annealing is required in harsh or complex forming.
10.4 Stamping
Duplex stainless steel is easy to stamp and form, but in many cases, components have been selected for austenitic stainless steel, carbon steel or ferritic stainless steel, and duplex stainless steel is used as an alternative to these materials. The first experiment usually does not change the thickness. Although the high strength of the duplex stainless steel allows the wall thickness to be reduced, the cost of redesign may outweigh the benefits of cost savings and weight reduction. In many cases, reducing the thickness is actually beneficial for forming However, in the first duplex stainless steel forming experiment, people often think that it is still a little "difficult".
When compared with the forming of carbon steel or ferritic stainless steel, the problems are almost all related to strength and springback. The yield strength of duplex stainless steel is 30%-50% higher, the work hardening of ferritic stainless steel is limited, and the operating load is relatively low. The strength of duplex stainless steel is high at the beginning, and then the strength becomes higher and higher, so rebound is a problem. On the other hand, duplex stainless steel is more plastic, and excessive bending will compensate for springback. Compared with ferritic stainless steels, duplex stainless steels are less sensitive to the direction of bending, which is related to the rolling direction. Due to the rolling of the duplex structure, the mechanical properties of the duplex stainless steel show some anisotropy, but because of the greater plasticity of the duplex structure, the actual effect is smaller than that of the ferritic steel.
The forming of ferritic stainless steel sheets often uses deep drawing. During operation, the steel plate is put into the mold and deforms in the thinnest place. In ferrite, this formability is greatly improved by the formation of metallographic texture. The behavior of duplex stainless steel sheets is rarely noticed, but it seems that this kind of favorable behavior cannot reach the same degree in the duplex structure. The deep drawing technology of duplex stainless steel may be significantly different from the practice of ferritic or austenitic stainless steel.
In the more general case, duplex stainless steels must be adjusted for both higher strength and lower ductility than austenitic stainless steels. The tensile forming performance of duplex stainless steel is limited by the ferrite phase, it does not have high work hardening performance, unlike austenitic stainless steel that can be extensively formed.
10.5 Spin forming
The strength and corrosion resistance of duplex stainless steels, especially chloride stress corrosion cracking resistance, make them candidates for rotating parts such as centrifugal equipment. Spin forming is an economical and commonly used method for manufacturing these parts.
Spin forming is a complicated operation, which depends largely on the quality of the equipment and the skill of the operator. Austenitic stainless steels are often spin-formed, but they usually require multiple intermediate annealings in the forming process to restore their plasticity. Limited experience in the spin forming of duplex stainless steels indicates that the forming load is very high, especially when the thickness of duplex stainless steels is not reduced relative to austenitic stainless steels. The use of equipment with sufficient power and strength for the spin forming of duplex stainless steel works well, but due to the low plasticity of duplex stainless steel, it requires more frequent intermediate annealing than austenitic stainless steel. Straightness and minimizing the "bulge" of the initial billet are important for spinning operations, but heavy mechanical leveling such as roll leveling may consume a portion of the plasticity in the first stage of spinning. Some duplex stainless steels are spin-formed above 650°C, followed by complete solution annealing.
11 Machining of duplex stainless steel
The yield strength of duplex stainless steels is generally twice that of non-nitrogen alloyed austenitic stainless steels, and their initial work hardening rate is at least comparable to that of common austenitic stainless steels. Duplex stainless steel has hard cutting debris and has an abrasive effect on the knife, and this is especially true of highly alloyed duplex stainless steel. Because the sulfur content is as low as possible in the production of duplex stainless steel, it does not help chip breaking.
For these reasons, duplex stainless steels are more difficult to machine than 300 series austenitic stainless steels that have the same corrosion resistance. Machining of duplex stainless steels generally requires greater cutting force and tool wear is faster. When using carbide cutting tools, the difficulty of machining is most obvious. Figure 15 shows the relative cutting performance index comparison of several duplex stainless steels and 316 stainless steels. Note that compared to 316 stainless steel, the economical duplex stainless steel S32101 has a higher machining performance level.
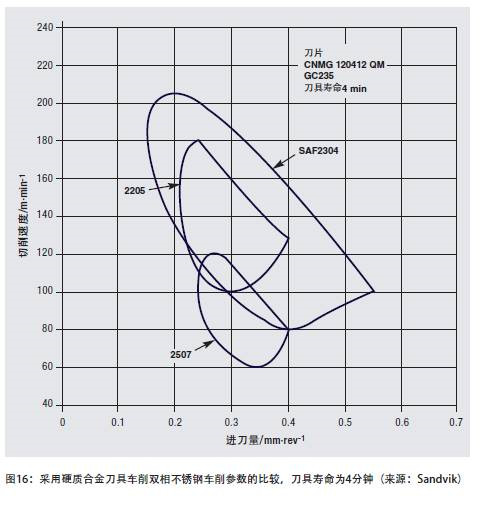
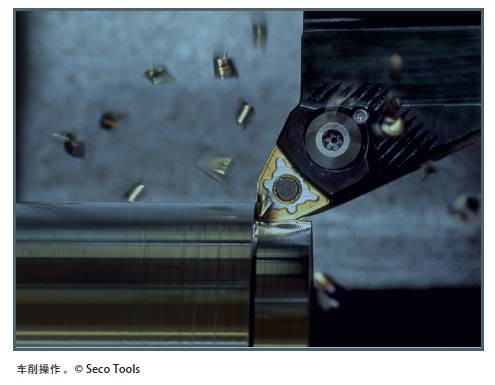
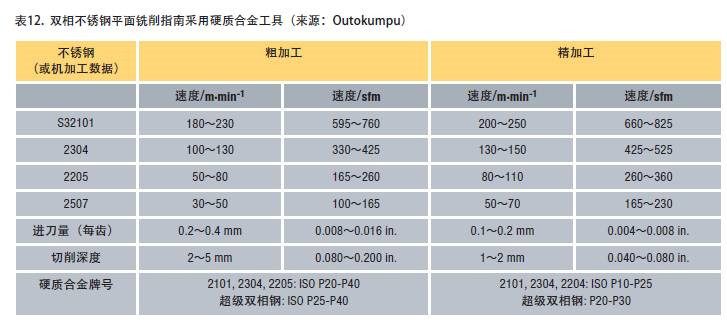
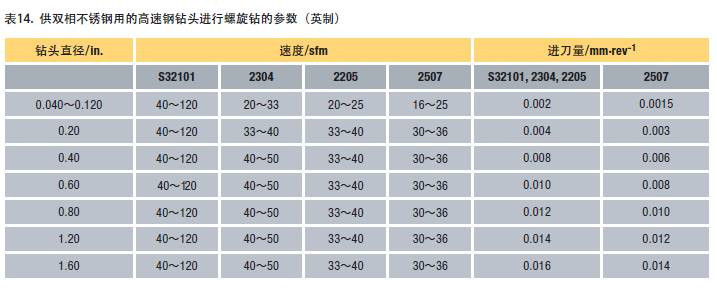
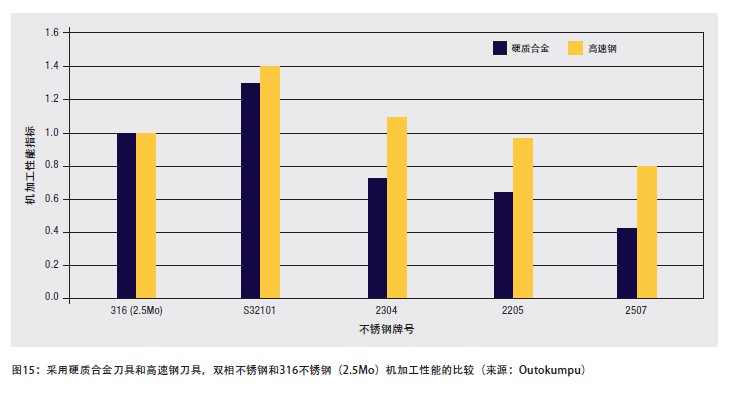
11.1 General principles of duplex stainless steel machining
The following machining principles apply to all stainless steels, but the importance of these principles must be emphasized for duplex stainless steels.
(1) Using high-power, sturdy equipment, the tool and the workpiece need to be firmly fixed (for the same cutting, the cutting force of duplex stainless steel is much larger than that of the corresponding austenitic stainless steel).
(2) Keep the extended portion of the tool as short as possible to minimize vibration.
(3) The radius of the protruding part of the tool is not greater than the necessary value.
(4) Choose a hard tool with a sharp shape, which has both a "sharp" blade and sufficient strength.
(5) Design the machining sequence so that the cutting depth is always below the work hardened layer formed by the first few cuts.
(6) The cutting speed should be large enough but not too fast to avoid cutting nodules and rapid wear.
(7) Change the blade of the cutter regularly or re-grind to ensure the sharpness of the blade.
(8) Use a large flow of coolant/lubricant, use cutting oil or an emulsion with extreme pressure (EP) additives.
(9) Use a carbide-coated insert with a chip groove shape.
11.2 Turning and planing
Many variables are involved in turning and planing operations, so it is impossible to give specific recommendations for all situations. Figure 16 and Table 11 give general guidelines for turning. Carbide cutting tools can be used for turning operations, allowing higher speeds than high-speed tool steels. However, more attention should be paid to the rigidity of cemented carbide tools and workpieces to avoid interruption of cutting.
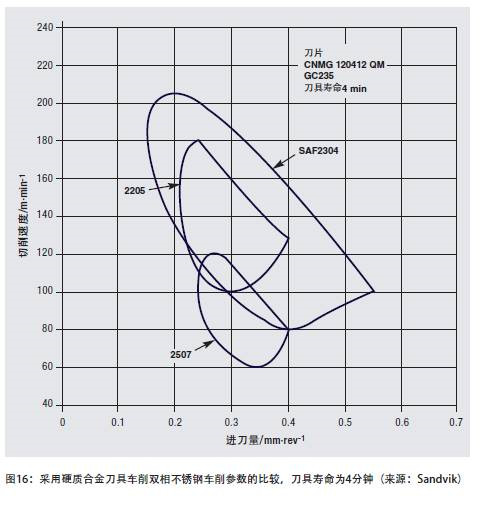
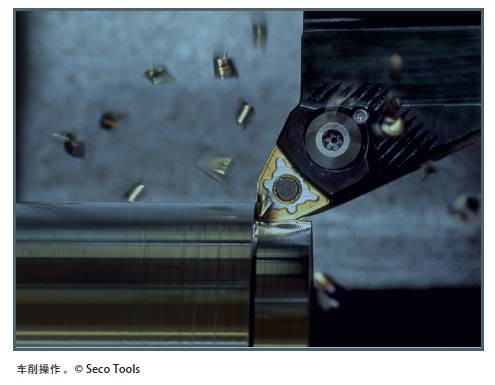
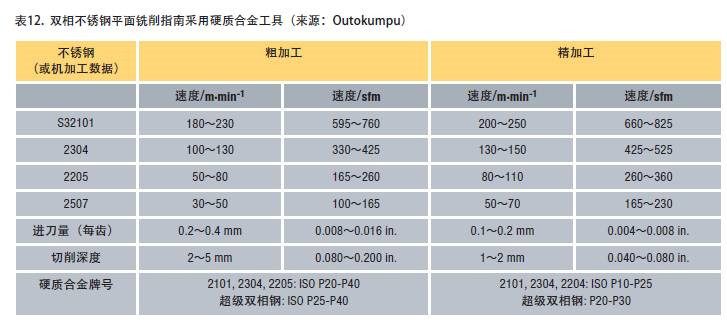
11.3 Plane milling with carbide tools
Guidelines for face milling of duplex stainless steel with carbide tools are shown in Table 12.
Coated inserts or high-toughness inserts are used for roughing. When finer finishing is required, harder inserts can be used.
With co-directional milling, the average chip thickness is at least 0.1 mm. As the infeed angle increases from 45° to 90°, the adjustment ratio factor for the amount of tooling is 1.0 to 0.7.
In order to allow chips to be ejected from the tool well, the machining process, especially during roughing, does not use coolant.
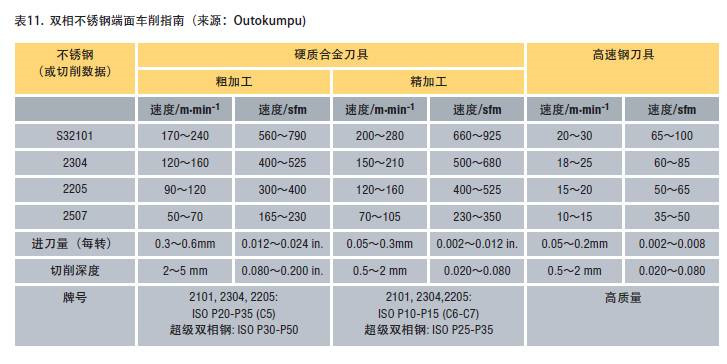
11.4 Use high-speed steel drill bit for auger drilling
Tables 13 and 14 give guidelines for auger drilling of duplex stainless steel with high-speed steel drills.
Drill shape: The top drill angle is 130°. It is recommended to use the self-centering drill shape. For large diameter drills, it is recommended to use a transverse edge.
Coolant: 10% of the emulsifier fully flows to the drill bit. For the case where the depth is greater than twice the diameter, the coolant is discharged through the hole regularly to discharge the chips.
Increased speed: TiN coating is used to increase the speed by 10%, and bit coolant is used to increase the speed by 10% to 20%.
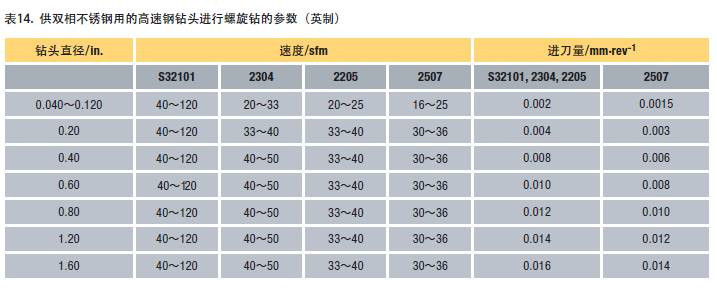
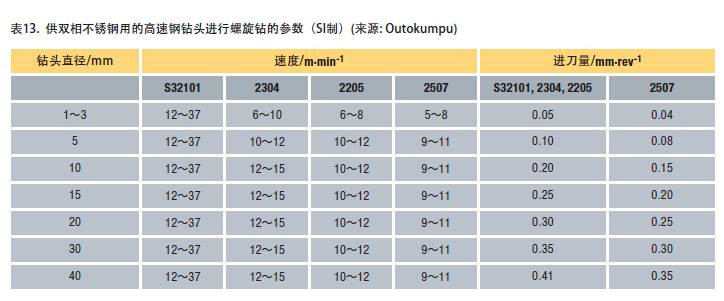
(To be continued)