Comparison of Cr12, Cr12MoV, Cr12Mo1V1 steel
Comparison of Cr12, Cr12MoV, Cr12Mo1V1
The difference between Cr12, Cr12MoV, and Cr12Mo1V1
Cr12, Cr12MoV, and Cr12Mo1V1 are all alloy tool steels with good hardenability and good wear resistance. Today we will introduce the main differences between Cr12, Cr12MoV and Cr12Mo1V1.
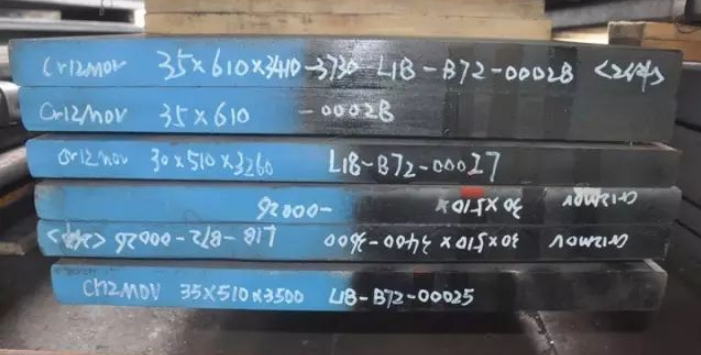
Comparison of chemical composition
Grade | Chemical composition | |||||||
C | Cr | Mo | V | Si | Mn | S | P | |
Cr12 | 2.00-2.30 | 11.5-13.0 | -- | -- | ≤0.40 | ≤0.40 | ≤0.03 | ≤0.03 |
Cr12MoV | 1.45-1.70 | 11.0-12.5 | 0.4-0.6 | 0.15-0.30 | ≤0.40 | ≤0.40 | ≤0.03 | ≤0.03 |
Cr12Mo1V1 | 1.40-1.60 | 11.0-13.0 | 0.70-1.20 | 0.5-1.1 | ≤0.60 | ≤0.60 | ≤0.03 | ≤0.03 |
By comparing the chemical composition of the three, the differences can be found as follows:
1. The carbon content of Cr12 is higher than that of Cr12MoV and Cr12Mo1V1.
2. Cr12 does not contain alloying elements, while Cr12MoV and Cr12Mo1V1 contain alloying elements Mo and V.
3. The Mo and V content of Cr12Mo1V1 is twice as high as that of Cr12MoV.
Performance comparison
1. Common points:
(1) High hardness can be obtained after quenching, reaching HRC60~63.
(2) It has high wear resistance.
(3) Hardenability oil quenching diameter (thickness) ≤ 300mm.
2. Differences:
Cr12
(1) Poor toughness due to the following reasons
a. High carbon and high chromium steel, with high hardness, high brittleness and low toughness after quenching.
b. There are many eutectic carbides, the distribution of carbides is uneven, and the tendency of segregation is serious, leading to a sharp decline in toughness.
c. There are no alloying elements Ni, Mo, V that improve toughness.
(2) It is not easy to perform wire cutting. Due to the residual stress in the material, wire cutting should be performed before heat treatment, and the wire cutting should be performed slowly.
Cr12MoV
(1) Good toughness, containing Mo and V alloy elements. It can be tempered at medium and high temperature to improve toughness during heat treatment. When tempering at 500-520℃, the hardness can reach HRC57-59.
(2) The wear resistance is better than Cr12, and it contains Mo and V carbides.
(3) The heat treatment deformation crack tendency is smaller than that of Cr12.
(4) After quenching and tempering, chemical heat treatment can be performed, gas nitrocarburizing or ion nitriding can be used, and the hardness can reach HRC60-65.
Cr12Mo1V1
(1) Cr12Mo1V1 has better toughness and wear resistance than Cr12MoV, because the content of Mo and V carbides is higher than that of Cr12MoV.
(2) The high temperature oxidation resistance is good, because Cr, Mo, V block the oxidation of Fe by O2, CO2, and H2O.
(3) The stress generated after wire cutting is less than Cr12MoV.
(4) The inhomogeneity of eutectic carbide is serious, which easily leads to carbide segregation.
The hazards of carbide segregation:
a. Increased crack tendency after quenching
b. Decreased bending strength
c. The crack tendency increases after wire cutting