Boiler hydraulic test
Boiler hydraulic test
What is a boiler hydraulic test?
Boiler hydraulic test is a test of strength and tightness with pressure water after the boiler is assembled.
When is the boiler hydraulic test conducted?
1. After the installation of the boiler is completed, the pressure-bearing parts shall undergo a hydraulic test.
2. After major and minor boiler repairs or local heating surface inspections, a conventional hydraulic test must be carried out. The test pressure is equal to the maximum allowable working pressure of the boiler. The hydraulic test shall be presided over by the maintenance personnel, and the operation and maintenance personnel shall participate together.
3. The boiler hydraulic test is generally performed twice for major and minor repairs, and the interval can be appropriately extended or shortened according to the specific technical status of the equipment and approved by the boiler supervision department of the group company. The overpressure test should be conducted in conjunction with major and minor repairs.
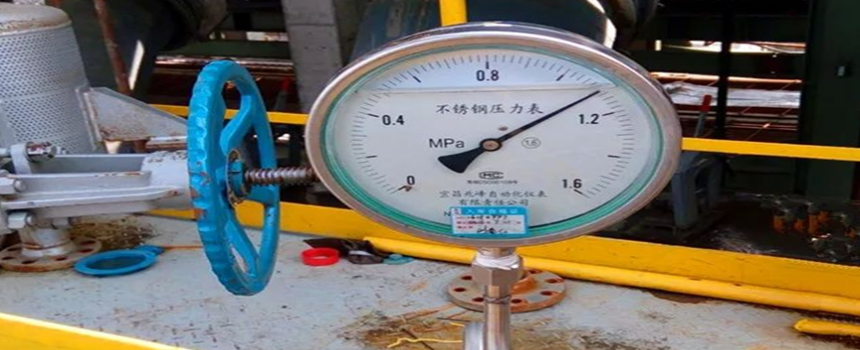
When should a boiler overpressure test be performed?
1. When the newly installed boiler is put into operation.
2. When the boiler that has been out of operation for more than one year resumes operation.
3. After the boiler is reformed and the pressure-bearing components have undergone major repairs or replacements, such as when the number of water-wall replacement tubes is more than 50%, the superheater, reheater, economizer and other components are replaced in groups, and the steam drum undergoes major repairs.
4. When the boiler's severe overpressure reaches 1.25 times the working pressure and above.
5. When the heating surface of the boiler is deformed in a large area after severe water shortage.
6. According to the operation situation, when there is doubt about the safety and reliability of the equipment operation.
Selection of boiler hydraulic test pressure (take a power plant as an example)
The pressures of the conventional hydraulic test and the overpressure test of the boiler are as follows: the superheater, the water wall, and the economizer are taken as a whole to perform the conventional hydraulic test with the drum working pressure of 19.79MPa, and the overpressure test is 1.5 times the drum working pressure 26.69 MPa) for the overpressure test; the reheater system is independently subjected to a hydrostatic test at 1.5 times (6.60 MPa) of the working pressure of the reheater inlet 4.4 MPa.
Scope of boiler hydraulic test
1. Superheated steam system: from the self-feeding water operation console to the main steam hydraulic test electric plug valve.
2. Reheat steam system: self-cooling and then importing hydraulic pressure test electric plugging valve to hot and then exporting hydraulic test plugging valve.
3. Pipe parts of the boiler body.
4. The steam drum water level gauge only participates in the conventional hydraulic test, not the overpressure test.
5. If Gauga has the operating conditions, Gaoka participates in the conventional hydraulic test and does not participate in the overpressure test.
6. The initial hydraulic test of the boiler body should be carried out before the boiler water pump motor body is installed. At this time, the pump casing participating in the hydraulic test is closed by a special water pressure blocking plate. Since the pump housing is open, the outlet valve (10) of each boiler water pump can be opened to fill the boiler with water in a symmetrical manner.
7. Before the hydraulic test in normal operation, the boiler water pump should be filled with water.
8. Overpressure test. The rotating parts of the boiler and boiler water pump should be installed after the overpressure hydraulic test is completed; the pump shell is isolated by the water pressure cover during the hydraulic test.
Inspection and preparation before hydraulic test
1. Check the steam-water system related to the boiler hydraulic test. The maintenance work has been completed, the work ticket is withdrawn, and the furnace and the flue are not working.
2. The steam drum and reheater inlets have been installed with an in-situ pressure gauge with a passing accuracy of 0.5, and the pressure gauges in the control room steam drum and reheater inlets are correctly calibrated. Good communication equipment.
3. Check that the boiler steam-water system has been reliably isolated from the turbine (Isolated according to the specific operation ticket).
4. During the hydrostatic test, the ambient temperature should be above 5 ℃, otherwise there should be reliable anti-freezing measures. The water temperature of the hydraulic test is generally 40 to 60 ℃, the difference between the temperature of the upper water and the temperature of the drum wall is not more than 28 ℃, and the temperature of the metal on the heated surface is not less than 21 ℃.
5. Dehydration water or condensed water is used for hydraulic test, and the PH value is about 10.0. The water used for the hydrostatic test of the reheater system has a chloride ion content of less than 0.2 mg / L to prevent the chloride ion from corroding the crystal.
6. The spring hanger of the pipeline within the scope of the hydraulic test should be fixed with a bolt or a positioning piece before the test. For the time being, the rigid hanger should be removed.
7. The superheater and reheater water-reducing water electric door is unlocked.
8. Contact maintenance to install temporary compression devices for all safety doors, the electromagnetic relief valve is out of the system, and the manual isolation door is closed to act during the waterproof pressure test.
9. The overhaul confirms that the debris in the pressure-bearing parts of the boiler is cleaned up before entering the water.
10. According to the operation rules of the feed pump, do a good job in the inspection and preparation of the electric feed pump.
11. Check the correct state of the boiler valves according to the hydraulic test check card.
Operation method of boiler hydraulic test
1. The hydraulic test shall be presided over by the person in charge of maintenance, the operating personnel shall be responsible for the operation, and the maintenance personnel shall be responsible for the inspection.
2. The sequence of hydraulic test: first make the reheat steam system, then the boiler main steam system; for the hydraulic test of the boiler valves, first make the second door, then make the first door.
3. During the hydraulic test of the superheated steam system, contact the thermal engineer to release the water level protection of the steam drum. First use the electric pump to fill the water, and after filling the water to the visible water level in the drum, change the water to the superheater secondary desuperheating water pipe. The water supply speed is not less than 2 hours in summer and not less than 4 hours in winter. When the water temperature is close to the drum wall temperature, the water supply speed can be appropriately increased.
4. When water continuously overflows from the air doors of the boiler, close the air release valves in the direction of water flow to increase pressure.
5. During the water supply process, closely monitor the water level changes, and check whether each component leaks, whether the expansion of the heated surface is normal. If an abnormality is found, the cause should be immediately identified and eliminated.
6. hydraulic test of reheater system: Inject water to the reheat system to boost pressure through the reheater accidental water spray. The pressure should be slow. When the pressure is below 1MPa, the speed of pressure boost is ≤0.1MPa / min. When the pressure reaches 1MPa, stop the inspection and continue the pressure boost for 15 minutes. The speed of boost is ≤0.3MPa / min, after the working pressure is 4.4MPa Stop the pressure increase and keep the pressure stable, carry out a comprehensive inspection of the reheater system, and then increase the pressure to 6.6MPa of the hydraulic test after no abnormality, and maintain the pressure for 5 minutes. After the hydraulic test passes, the pressure will be reduced to work Pressure, water discharge and pressure relief, pressure reduction rate is 0.3MPa / min.
7. hydraulic test of boiler main steam system: use superheater temperature-reducing water regulating door to increase pressure, the pressure should be slow, the pressure increase speed below 9.8MPa is less than or equal to 0.3MPa / min, when the pressure rises to 2MPa, the pressure increase is suspended Check, there is no abnormality, continue to increase pressure after 15 minutes of constant pressure, suspend the pressure increase when it is increased to 5.88MPa, observe the pressure change, if there is no abnormality, continue to increase the pressure to 9.8MPa, and then increase the pressure at ≤0.2MPa / min, When boosting to 11.77MPa, stop boosting and check for abnormalities. After no abnormality, continue to increase the pressure to the working pressure of the steam drum at 19.79MPa. After keeping the pressure for 5 minutes, close the water inlet valve, record the pressure drop value within 5 minutes after the water inlet valve is closed, and notify the maintenance to conduct a comprehensive inspection.
8. If the overpressure test is carried out, the water level gauge of the steam drum should be taken out. After the inspection is normal, continue to increase the pressure to the overpressure test pressure at the same speed to 29.69MPa, hold for 30 minutes, use a trap at a speed of 0.3MPa / min When the pressure is relieved, when the working pressure of the steam drum is closed, the trap is closed to maintain the conventional test pressure and a comprehensive inspection is carried out.
9. After the hydraulic test is completed, use a row or trap to relieve the pressure, and the pressure reduction rate is 0.3MPa / min.
10. When the pressure drops to 0.2MPa, open the air doors and traps to discharge water. If the boiler is ready for operation and the water quality is qualified, it can be placed to the ignition level, otherwise all the water should be released and re-inlet. The superheater, main steam pipeline, and reheater should drain the collected water. Notify the maintenance to release the safety door pressing device.
11. If the boiler is not put into operation in a short period of time, close the pressure relief door and perform maintenance in accordance with the furnace shutdown maintenance regulations.
Qualified standard for hydraulic test
1. Qualified standard for working pressure hydraulic test: when the hydraulic test is increased to the specified pressure, close the water inlet valve for 5 minutes, and record the pressure drop value. There should be no traces of water bead and water mist leakage at the weld. There is no obvious residual deformation of the pressure element.
2. Eligibility criteria for the overpressure test: the metal walls and welds of the pressured components are free of any traces of water droplets and water mist. There is no obvious residual deformation of the pressure element.
Notes on hydraulic test
1. During the hydrostatic test, the ambient temperature is not lower than 5 ℃. If the ambient temperature is lower than 5 ℃, anti-freezing measures must be taken.
2. Before the hydraulic test enters the water, the air doors on each pressure-bearing component must be fully opened, and the air doors should be closed one by one after the air is exhausted and water continues to emerge.
3. During the hydrostatic test, adjust the water intake or pressure relief slowly to prevent sudden pressure changes.
4. There must be someone to monitor and adjust the boosting process. When the pressure is close to the test pressure, the boosting speed should be slowed down to prevent overpressure.
5. During the overpressure test, the inspection shall not be carried out before the pressure has dropped to the working pressure. The inspection shall not be carried out until the pressure has dropped to the working pressure.
6. Before the boiler hydraulic test, the steam turbine crank must be put into continuous operation.
7. Before the hydraulic test, the boiler test system should be reliably isolated from the turbine, and safety measures should be taken to prevent the isolation valve from being opened by mistake. During the test, the cylinder temperature should be closely monitored for changes. 8. During the overpressure test, the steam drum water level gauge should be out of the system, and all safety valves must be equipped with plugs for isolation. After the hydraulic test is completed, remove the safety door plug and the pin of the spring hanger.
9. It is forbidden to use the boiler water pump drain valve to discharge the pressure of the furnace body and prevent the boiler water from entering the motor chamber.
10. Water treated with solid chemicals should not be used as water for hydrostatic testing to prevent solids from settling in the superheater or reheater.
11. Before filling the boiler, make sure that all foreign substances in the drum and header are eliminated.
12. The rotating parts (impeller, motor, etc.) of the boiler water circulation pump should be installed after the hydraulic test is completed. When the water pressure is applied, the pump casing is blocked by a special hydraulic pressure blocking plate. The outlet valve of the circulation pump should be opened during water filling to speed up the boiler water filling.
13. Before conducting the hydraulic test higher than the normal operating pressure, all safety valves should be fitted with plugs or compression devices.
14. If the boiler is filled with water through the economizer, the economizer recirculation line valve should be fully open, so that it is easy to fill with water and can minimize the air trapped.
What is a boiler hydraulic test?
Boiler hydraulic test is a test of strength and tightness with pressure water after the boiler is assembled.
When is the boiler hydraulic test conducted?
1. After the installation of the boiler is completed, the pressure-bearing parts shall undergo a hydraulic test.
2. After major and minor boiler repairs or local heating surface inspections, a conventional hydraulic test must be carried out. The test pressure is equal to the maximum allowable working pressure of the boiler. The hydraulic test shall be presided over by the maintenance personnel, and the operation and maintenance personnel shall participate together.
3. The boiler hydraulic test is generally performed twice for major and minor repairs, and the interval can be appropriately extended or shortened according to the specific technical status of the equipment and approved by the boiler supervision department of the group company. The overpressure test should be conducted in conjunction with major and minor repairs.
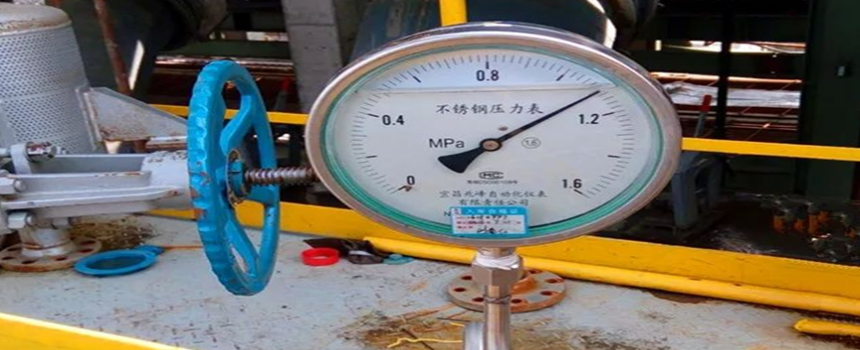
When should a boiler overpressure test be performed?
1. When the newly installed boiler is put into operation.
2. When the boiler that has been out of operation for more than one year resumes operation.
3. After the boiler is reformed and the pressure-bearing components have undergone major repairs or replacements, such as when the number of water-wall replacement tubes is more than 50%, the superheater, reheater, economizer and other components are replaced in groups, and the steam drum undergoes major repairs.
4. When the boiler's severe overpressure reaches 1.25 times the working pressure and above.
5. When the heating surface of the boiler is deformed in a large area after severe water shortage.
6. According to the operation situation, when there is doubt about the safety and reliability of the equipment operation.
Selection of boiler hydraulic test pressure (take a power plant as an example)
The pressures of the conventional hydraulic test and the overpressure test of the boiler are as follows: the superheater, the water wall, and the economizer are taken as a whole to perform the conventional hydraulic test with the drum working pressure of 19.79MPa, and the overpressure test is 1.5 times the drum working pressure 26.69 MPa) for the overpressure test; the reheater system is independently subjected to a hydrostatic test at 1.5 times (6.60 MPa) of the working pressure of the reheater inlet 4.4 MPa.
Scope of boiler hydraulic test
1. Superheated steam system: from the self-feeding water operation console to the main steam hydraulic test electric plug valve.
2. Reheat steam system: self-cooling and then importing hydraulic pressure test electric plugging valve to hot and then exporting hydraulic test plugging valve.
3. Pipe parts of the boiler body.
4. The steam drum water level gauge only participates in the conventional hydraulic test, not the overpressure test.
5. If Gauga has the operating conditions, Gaoka participates in the conventional hydraulic test and does not participate in the overpressure test.
6. The initial hydraulic test of the boiler body should be carried out before the boiler water pump motor body is installed. At this time, the pump casing participating in the hydraulic test is closed by a special water pressure blocking plate. Since the pump housing is open, the outlet valve (10) of each boiler water pump can be opened to fill the boiler with water in a symmetrical manner.
7. Before the hydraulic test in normal operation, the boiler water pump should be filled with water.
8. Overpressure test. The rotating parts of the boiler and boiler water pump should be installed after the overpressure hydraulic test is completed; the pump shell is isolated by the water pressure cover during the hydraulic test.
Inspection and preparation before hydraulic test
1. Check the steam-water system related to the boiler hydraulic test. The maintenance work has been completed, the work ticket is withdrawn, and the furnace and the flue are not working.
2. The steam drum and reheater inlets have been installed with an in-situ pressure gauge with a passing accuracy of 0.5, and the pressure gauges in the control room steam drum and reheater inlets are correctly calibrated. Good communication equipment.
3. Check that the boiler steam-water system has been reliably isolated from the turbine (Isolated according to the specific operation ticket).
4. During the hydrostatic test, the ambient temperature should be above 5 ℃, otherwise there should be reliable anti-freezing measures. The water temperature of the hydraulic test is generally 40 to 60 ℃, the difference between the temperature of the upper water and the temperature of the drum wall is not more than 28 ℃, and the temperature of the metal on the heated surface is not less than 21 ℃.
5. Dehydration water or condensed water is used for hydraulic test, and the PH value is about 10.0. The water used for the hydrostatic test of the reheater system has a chloride ion content of less than 0.2 mg / L to prevent the chloride ion from corroding the crystal.
6. The spring hanger of the pipeline within the scope of the hydraulic test should be fixed with a bolt or a positioning piece before the test. For the time being, the rigid hanger should be removed.
7. The superheater and reheater water-reducing water electric door is unlocked.
8. Contact maintenance to install temporary compression devices for all safety doors, the electromagnetic relief valve is out of the system, and the manual isolation door is closed to act during the waterproof pressure test.
9. The overhaul confirms that the debris in the pressure-bearing parts of the boiler is cleaned up before entering the water.
10. According to the operation rules of the feed pump, do a good job in the inspection and preparation of the electric feed pump.
11. Check the correct state of the boiler valves according to the hydraulic test check card.
Operation method of boiler hydraulic test
1. The hydraulic test shall be presided over by the person in charge of maintenance, the operating personnel shall be responsible for the operation, and the maintenance personnel shall be responsible for the inspection.
2. The sequence of hydraulic test: first make the reheat steam system, then the boiler main steam system; for the hydraulic test of the boiler valves, first make the second door, then make the first door.
3. During the hydraulic test of the superheated steam system, contact the thermal engineer to release the water level protection of the steam drum. First use the electric pump to fill the water, and after filling the water to the visible water level in the drum, change the water to the superheater secondary desuperheating water pipe. The water supply speed is not less than 2 hours in summer and not less than 4 hours in winter. When the water temperature is close to the drum wall temperature, the water supply speed can be appropriately increased.
4. When water continuously overflows from the air doors of the boiler, close the air release valves in the direction of water flow to increase pressure.
5. During the water supply process, closely monitor the water level changes, and check whether each component leaks, whether the expansion of the heated surface is normal. If an abnormality is found, the cause should be immediately identified and eliminated.
6. hydraulic test of reheater system: Inject water to the reheat system to boost pressure through the reheater accidental water spray. The pressure should be slow. When the pressure is below 1MPa, the speed of pressure boost is ≤0.1MPa / min. When the pressure reaches 1MPa, stop the inspection and continue the pressure boost for 15 minutes. The speed of boost is ≤0.3MPa / min, after the working pressure is 4.4MPa Stop the pressure increase and keep the pressure stable, carry out a comprehensive inspection of the reheater system, and then increase the pressure to 6.6MPa of the hydraulic test after no abnormality, and maintain the pressure for 5 minutes. After the hydraulic test passes, the pressure will be reduced to work Pressure, water discharge and pressure relief, pressure reduction rate is 0.3MPa / min.
7. hydraulic test of boiler main steam system: use superheater temperature-reducing water regulating door to increase pressure, the pressure should be slow, the pressure increase speed below 9.8MPa is less than or equal to 0.3MPa / min, when the pressure rises to 2MPa, the pressure increase is suspended Check, there is no abnormality, continue to increase pressure after 15 minutes of constant pressure, suspend the pressure increase when it is increased to 5.88MPa, observe the pressure change, if there is no abnormality, continue to increase the pressure to 9.8MPa, and then increase the pressure at ≤0.2MPa / min, When boosting to 11.77MPa, stop boosting and check for abnormalities. After no abnormality, continue to increase the pressure to the working pressure of the steam drum at 19.79MPa. After keeping the pressure for 5 minutes, close the water inlet valve, record the pressure drop value within 5 minutes after the water inlet valve is closed, and notify the maintenance to conduct a comprehensive inspection.
8. If the overpressure test is carried out, the water level gauge of the steam drum should be taken out. After the inspection is normal, continue to increase the pressure to the overpressure test pressure at the same speed to 29.69MPa, hold for 30 minutes, use a trap at a speed of 0.3MPa / min When the pressure is relieved, when the working pressure of the steam drum is closed, the trap is closed to maintain the conventional test pressure and a comprehensive inspection is carried out.
9. After the hydraulic test is completed, use a row or trap to relieve the pressure, and the pressure reduction rate is 0.3MPa / min.
10. When the pressure drops to 0.2MPa, open the air doors and traps to discharge water. If the boiler is ready for operation and the water quality is qualified, it can be placed to the ignition level, otherwise all the water should be released and re-inlet. The superheater, main steam pipeline, and reheater should drain the collected water. Notify the maintenance to release the safety door pressing device.
11. If the boiler is not put into operation in a short period of time, close the pressure relief door and perform maintenance in accordance with the furnace shutdown maintenance regulations.
Qualified standard for hydraulic test
1. Qualified standard for working pressure hydraulic test: when the hydraulic test is increased to the specified pressure, close the water inlet valve for 5 minutes, and record the pressure drop value. There should be no traces of water bead and water mist leakage at the weld. There is no obvious residual deformation of the pressure element.
2. Eligibility criteria for the overpressure test: the metal walls and welds of the pressured components are free of any traces of water droplets and water mist. There is no obvious residual deformation of the pressure element.
Notes on hydraulic test
1. During the hydrostatic test, the ambient temperature is not lower than 5 ℃. If the ambient temperature is lower than 5 ℃, anti-freezing measures must be taken.
2. Before the hydraulic test enters the water, the air doors on each pressure-bearing component must be fully opened, and the air doors should be closed one by one after the air is exhausted and water continues to emerge.
3. During the hydrostatic test, adjust the water intake or pressure relief slowly to prevent sudden pressure changes.
4. There must be someone to monitor and adjust the boosting process. When the pressure is close to the test pressure, the boosting speed should be slowed down to prevent overpressure.
5. During the overpressure test, the inspection shall not be carried out before the pressure has dropped to the working pressure. The inspection shall not be carried out until the pressure has dropped to the working pressure.
6. Before the boiler hydraulic test, the steam turbine crank must be put into continuous operation.
7. Before the hydraulic test, the boiler test system should be reliably isolated from the turbine, and safety measures should be taken to prevent the isolation valve from being opened by mistake. During the test, the cylinder temperature should be closely monitored for changes. 8. During the overpressure test, the steam drum water level gauge should be out of the system, and all safety valves must be equipped with plugs for isolation. After the hydraulic test is completed, remove the safety door plug and the pin of the spring hanger.
9. It is forbidden to use the boiler water pump drain valve to discharge the pressure of the furnace body and prevent the boiler water from entering the motor chamber.
10. Water treated with solid chemicals should not be used as water for hydrostatic testing to prevent solids from settling in the superheater or reheater.
11. Before filling the boiler, make sure that all foreign substances in the drum and header are eliminated.
12. The rotating parts (impeller, motor, etc.) of the boiler water circulation pump should be installed after the hydraulic test is completed. When the water pressure is applied, the pump casing is blocked by a special hydraulic pressure blocking plate. The outlet valve of the circulation pump should be opened during water filling to speed up the boiler water filling.
13. Before conducting the hydraulic test higher than the normal operating pressure, all safety valves should be fitted with plugs or compression devices.
14. If the boiler is filled with water through the economizer, the economizer recirculation line valve should be fully open, so that it is easy to fill with water and can minimize the air trapped.