ASTM A668/A668M Standard
ASTM A668/A668M
Standard Specification for
Steel Forgings, Carbon and Alloy, for General Industrial Use
1. Scope*
1.1 This specification covers untreated and heat-treated carbon and alloy steel forgings for general industrial use. Other ASTM specifications for forgings are available for specific applications such as pressure vessels, railroad use, turbine generators, gearing, and others involving special temperature requirements.
1.2 Hot-rolled or cold finished bars are not within the scope of this specification.
1.3 Six classes of carbon steel and seven classes of alloy steel forgings are listed (see Section 7), which indicates their required heat treatments, as well as mechanical properties.
1.4 Provision, with the suffix H for certification and marking, for the supply of forgings after hardness testing only.
1.5 Supplementary requirements, including those in Specification A788/A788M, of an optional nature are provided.These shall apply only when specified by the purchaser.
1.6 Appendix X1 lists the current classes corresponding to the various classes of Specifications A235, A237, and A243,which have been superseded by this specification.
1.7 The values stated in either SI units or inch-pound units are to be regarded separately as standard; within the text and tables, the SI units are shown in brackets. The values stated in each system may not be exact equivalents; therefore, each system shall be used independently of the other. Combining values from the two systems may result in nonconformance with the standard.
1.8 Unless the order specifies the applicable "M" specification, the forgings shall be furnished to the inch-pound units.
2. Referenced Documents
2.1 ASTM Standards:
A275/A275M Practice for Magnetic Particle Examination of Steel Forgings
A370 Test Methods and Definitions for Mechanical Testing of Steel Products
A388/A388M Practice for Ultrasonic Examination of Steel Forgings
A788/A788M Specification for Steel Forgings, General Requirements
E290 Test Methods for Bend Testing of Material for Ductility
E381 Method of Macroetch Testing Steel Bars, Billets,Blooms, and Forgings
3. Terminology
3.1 The terminology section of Specification A788/A788M is applicable to this specification.
3.2 Definitions of Terms Specific to This Standard:
3.2.1 class—a description of steel forgings based on heat treatment, mechanical properties and composition.
3.2.2 controlling cross section thickness (T C )—the diameter of the largest theoretical sphere which can be inscribed within the volume of the forging.
3.2.3 T P —designates prolongations which have a size other than the controlling cross section thickness (T C ).
4. Ordering Information and General Requirements
4.1 Material supplied to this specification shall conform to the requirements of Specification A788/A788M which outlines additional ordering information, manufacturing requirements,testing and retesting methods and procedures, marking,certification, product analysis variations and additional supplementary requirements.
4.1.1 If the requirements of this specification are in conflict with the requirements of Specification A788/A788M, the requirements of this specification shall prevail.
4.2 When this specification is to be applied to an inquiry,contract, or order, the purchaser should furnish the following information:
4.2.1 The ordering information required by Specification A788/A788M,
4.2.2 The class of forging desired as listed in Table 1,
4.2.3 Location(s) of areas of significant loading if test specimens are to be located in accordance with 7.1.4.5,
4.2.4 The options which may be selected as found in 5.3.2,6.1, and 7.3, and
4.2.5 Any applicable supplementary requirements.
5. Materials and Manufacture
5.1 Discard—Sufficient discard shall be made from each ingot to secure freedom from piping and undue segregation.
5.2 Forging Process:
5.2.1 The forging shall be brought as close as practical to finished shape and size by hot mechanical work.
5.2.2 Supplementary requirements S2, S14, and S15 may be specified by the purchaser to satisfy concerns about the utility of the proposed forging.
5.3 Heat Treatment:
5.3.1 All forgings, other than Class A, shall be heat treated.See Section 7.
5.3.2 Where options exist within a class, the choice of heat treatment shall be left to the discretion of the manufacturer,unless the purchaser specifies one of the available options.
6. Chemical Composition
6.1 The steel shall conform to the requirements prescribed in Table 1.
6.2 The choice of chemical composition is left to the discretion of the manufacturer, unless otherwise specified by the purchaser. See Appendix X2.
6.3 Heat Analysis:
6.3.1 An analysis of each heat shall be made by the manufacturer.
6.4 Product Analysis—An analysis may be made by the purchaser according to the requirements of Specification A788/A788M. If a standard grade has been used to manufacture the forging the permissible variations in composition of Specification A788/A788M shall apply. If a non-standard grade of steel has been used, and composition limits have not been supplied, the product analysis can be used only to confirm the type of steel supplied.
7. Mechanical Properties
7.1 Tensile Requirements:
7.1.1 The material shall conform to the tensile properties prescribed in Table 2. See Test Methods A370.
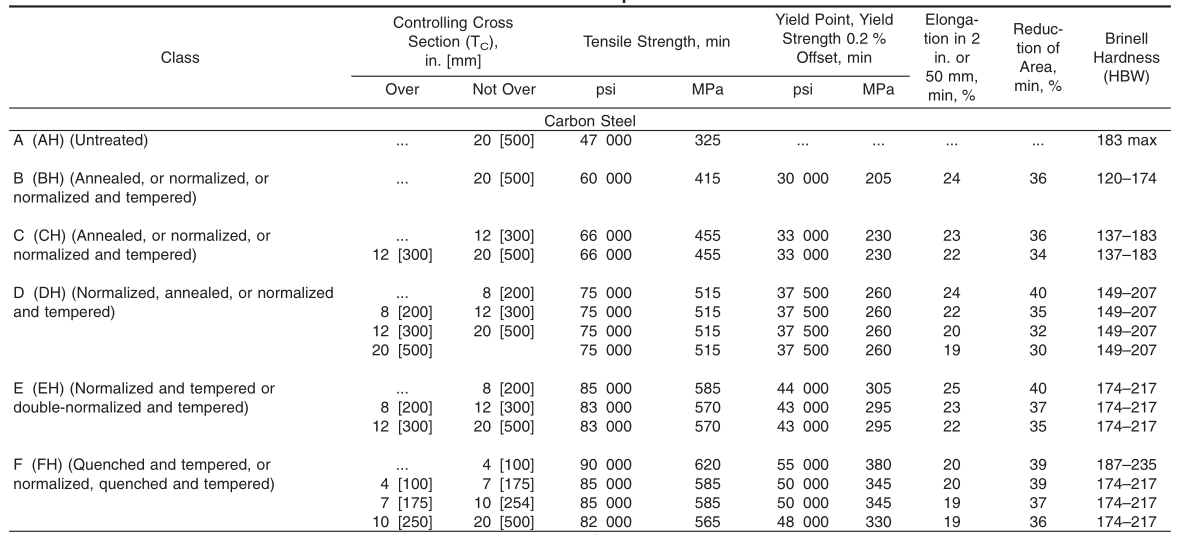
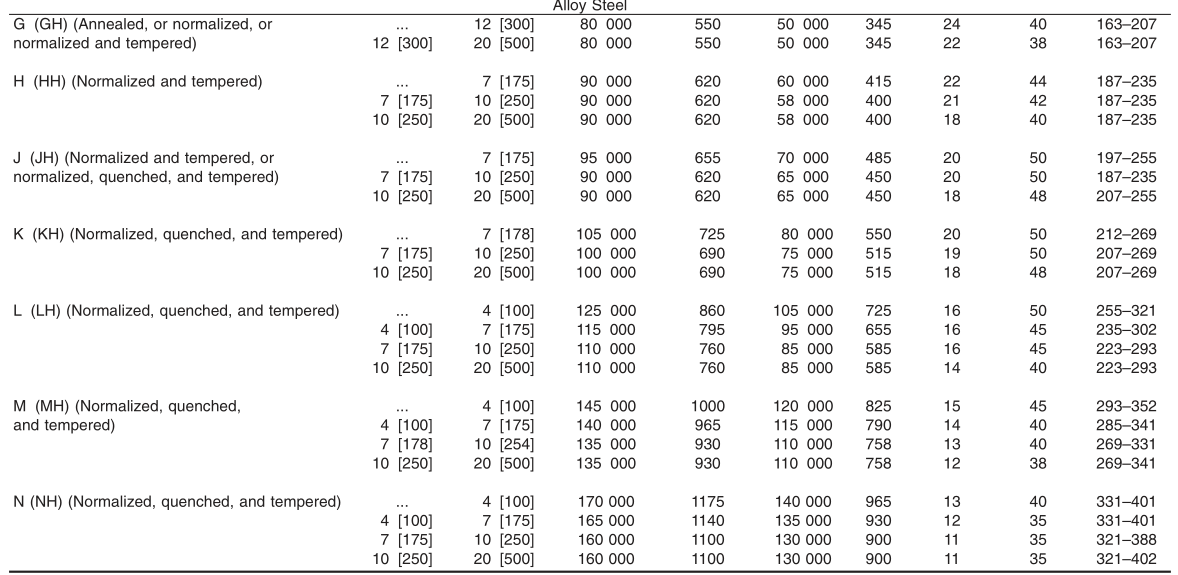
A Forgings with controlling cross section thickness (T C ) in excess of 20 in. [508 mm] for all classes other than class D may be certified to Specification A668/A668M provided they meet the requirements for controlling cross sections of 20 in. [508 mm] listed in Table 2. Alternatively, the manufacturer and purchaser may agree upon the required mechanical property values as described in Supplement S9.1.
B Requirements presented in Table 2 are to be met at the test locations given in 7.1.4. Tests from other locations may not exhibit the property values shown in Table 2.
7.1.2 All Forgings—The dimensions of the controlling cross section thickness (T C ) of the forging at time of heat treatment determine the mechanical properties to be met within each class (see Table 2) except as noted in 7.1.4.2.
7.1.3 Number of Tests—Unless the purchaser specifies that forgings shall be furnished in accordance with the requirements of 7.3, the number of tension tests performed shall be as follows:
7.1.3.1 For all classes of heat-treated forgings with as-heat treated weights (excluding test prolongations) less than 5000 lb [2250 kg] each, one test shall be made from each size classification represented in each heat in each annealing or normalizing charge, or from each size classification in each heat in each normalizing or quenching charge represented in each tempering charge. For untreated forgings (Class A)weighing less than 5000 lb [2250 kg] each, one test from each heat shall be made.
7.1.3.2 On all classes, for forgings with as-heat treated weights (excluding test prolongations) of 5000 lb [2250 kg] or more, at least one test from each forging shall be made.
7.1.3.3 On all classes, for forgings with as-heat treated weights (excluding test prolongations) of 7000 lb [3200 kg] or more, two tests will be taken: on ring and disk forgings 180° apart; on shafts and long hollow cylinders (over 80 in. [2.0 m] in length excluding test material), one from each end and offset 180°. Shafts and cylinder forgings 80 in. [2.0 m] or less in length (excluding test material) may have both tests located at one end 180° apart.
7.1.3.4 When forgings are made in multiple as a single forging, that is, forged as one piece and divided after heat treatment, the multiple forging shall be considered as one forging, and the number of tests required shall be as designated in 7.1.3.1, 7.1.3.2, and 7.1.3.3.
7.1.4 Prolongations:
7.1.4.1 A sufficient number of the forgings shall have prolongations for extracting specimens for testing. Examples of test locations for various forging configurations are shown in Figs. 1 and 2.

NOTE 1—Figures provided demonstrate the concept of controlling cross section thickness (T C ) but do not encompass all possible test prolongation configurations which meet the requirements of Section 7.
7.1.4.2 For all forgings of non-uniform cross section in classes A, B, C, D, E, G and H: The prolongation(s) may be extensions of sections other than the controlling cross section thickness (T C ), that is T P ≠ T C . In this case, the dimension of T P shall determine the mechanical properties to be met within each class. When T P ≠ T C , T P shall not have more reduction than the smallest cross section to be qualified.
(1) For annealed, normalized, or normalized and tempered forgings in classes A, B, C, D, E, G and H the center of the gage length axis of tension test specimens shall be 1 ⁄ 4 the controlling cross section thickness (T C ) from one surface except as noted in 7.1.4.2 (2).
(2) If the prolongation thickness (T P ) is less than the controlling cross section thickness (T C ) the center of the gage length axis of the tension test shall be ¼ of the prolongation thickness (T P ) from one surface.
7.1.4.3 For quenched forgings in Classes F, J, K, L, M, and N, the center of the gage length axis of the tension test specimen shall be at a minimum 1 ⁄ 4 (T C ) from one quenched surface and 3 1 ⁄ 2 in. [90 mm] from all other quenched surfaces.
7.1.4.4 In place of prolongations, the manufacturer may: (1) elect to submit a representative forging(s) to represent each test lot; in this event, the representative forging must be made from the same heat of steel, must not receive more reduction than the forging it represents, must receive the same type of hot working it represents, be of the same controlling cross section thickness (T C ), and have been heat treated in the same furnace charge as the forging(s) it represents; or (2) obtain the test specimen from the trepanned material of transverse or radial holes, provided the required depth is met.
7.1.4.5 With prior purchaser approval, test specimens may be taken at a depth (t) corresponding to the distance from the area of significant stress to the nearest heat treated surface and at least twice this distance (2t) from any second surface.However, the test depth shall not be nearer to one heat-treated surface than 3 ⁄ 4 in. [19 mm] and to the second heat treated surface than 1 1 ⁄ 2 in. [38 mm]. Sketches showing the exact test locations shall be approved by the purchaser when this method is used.
7.1.5 Tests for acceptance shall be made after final heat treatment of the forgings. Thermal cycling after mechanical testing is complete shall not exceed 50°F [30°C] less than the temperature used to establish mechanical properties.
7.1.6 Test specimen orientation relative to the axis of major metal flow is to be at the discretion of the manufacturer provided the requirements of Table 2 are met. Test specimen orientation shall be reported.
7.1.7 Yield point shall be determined on carbon steel Grades Athrough F, and yield strength on alloy steel Grades G through N. For carbon steel grades not showing a yield point, the yield strength at 0.2 % offset shall be reported.
7.2 Hardness Tests—Brinell hardness tests shall be performed after heat treatment (except on Class A forgings) and rough machining on each forging weighing under 7000 lb [3200 kg] at the time of heat treatment and each multiple forging made in accordance with 7.1.3.3 weighing under 7000 lb [3200 kg] at the time of heat treatment.
7.2.1 Hardness testing on forgings in excess of 7000 lb [3200 kg] at the time of heat treatment may be omitted provided they meet the tensile requirements of Table 2. For additional exceptions see 7.1.3.4 and 7.3.
7.2.2 When ordered without rough machining, hardness measurements shall be conducted on the forgings after heat treatment. Due consideration should be provided for the removal of oxidation and decarburization to ensure accuracy of hardness results when forgings which have not been rough machined are evaluated.
7.2.3 The average value of the hardness readings on each forging shall fall within the hardness ranges specified in Table 2. The permissible variation in hardness in any forging over 250 lb [110 kg] shall not exceed 30 HBW for ClassesAthrough E, 40 HB for Classes F through J, 50 HB for Classes K through N.
7.2.4 At least two hardness tests shall be taken on each flat face of disks, rings, and hollow forgings over 250 lb [110 kg] approximately at mid-radius and 180° apart, for example, at the 3:00 and 9:00 positions on one face, and 6:00 and 12:00 positions on the opposite face. On solid forgings over 250 lb [110 kg], at least four tests shall be taken on the periphery of the forging, two at each end 180° apart.
7.2.5 For forgings 250 lb [110 kg] and less, Brinell testing shall be performed on the broken test specimens representing the heat or heats included in each heat treating charge, or in the case of untreated forgings (Class A), on the test specimen representing each heat. The results shall meet the requirements of Table 2. If the purchaser desires Brinell testing of each forging, Supplementary Requirement S11 may be used.
7.3 If so specified by the purchaser, forgings may be supplied on the basis of hardness tests alone. If this option is exercised, the class shall be identified in certification and marking with the suffix “H,” that is, “AH,” “BH,” “CH,” etc.
8. Retreatment
8.1 When heat-treated forgings are specified, and the mechanical test results of any test lot do not conform to the requirements specified, the manufacturer may re-austenitize the lot not more than three additional times, and retests shall be made according to Section 7. Multiple retempering is not precluded by this requirement.
8.2 When untreated forgings (ClassA) are specified, and the mechanical test results of any test lot do not conform to the requirements specified, the manufacturer may anneal,normalize, or normalize and temper, one or more times, but not more than three times; and retests shall be made in accordance with Section 7. The tensile properties shall conform to the requirements for the class of forgings ordered (Class A).
9. Inspection, Rejection, and Certification
9.1 Facilities for inspection at the place of manufacture,rejection of forgings and certification shall comply with Specification A788/A788M.
10. Product Marking
10.1 The marking requirements of Specification A788/A788M shall be augmented as follows.
10.2 Each forging over 250 lb [110 kg] shall be legibly stamped by the manufacturer with the manufacturer’s name or trademark, the manufacturer’s serial number, the specification identification number, followed by the appropriate class number and, where applicable, a standard Grade designation.
10.3 For forgings 250 lb [110 kg] and under, the purchaser may indicate the nature and location of identification marks.
10.4 The type of stamps to be used shall be round-nosed or “interrupted-dot” die stamps having a minimum radius of 1 ⁄ 32
in. [0.79 mm].
11. Keywords
11.1 alloy steel forgings; carbon steel forgings; general industrial applications; heat treatment classifications; strength classifications
Standard Specification for
Steel Forgings, Carbon and Alloy, for General Industrial Use
1. Scope*
1.1 This specification covers untreated and heat-treated carbon and alloy steel forgings for general industrial use. Other ASTM specifications for forgings are available for specific applications such as pressure vessels, railroad use, turbine generators, gearing, and others involving special temperature requirements.
1.2 Hot-rolled or cold finished bars are not within the scope of this specification.
1.3 Six classes of carbon steel and seven classes of alloy steel forgings are listed (see Section 7), which indicates their required heat treatments, as well as mechanical properties.
1.4 Provision, with the suffix H for certification and marking, for the supply of forgings after hardness testing only.
1.5 Supplementary requirements, including those in Specification A788/A788M, of an optional nature are provided.These shall apply only when specified by the purchaser.
1.6 Appendix X1 lists the current classes corresponding to the various classes of Specifications A235, A237, and A243,which have been superseded by this specification.
1.7 The values stated in either SI units or inch-pound units are to be regarded separately as standard; within the text and tables, the SI units are shown in brackets. The values stated in each system may not be exact equivalents; therefore, each system shall be used independently of the other. Combining values from the two systems may result in nonconformance with the standard.
1.8 Unless the order specifies the applicable "M" specification, the forgings shall be furnished to the inch-pound units.
2. Referenced Documents
2.1 ASTM Standards:
A275/A275M Practice for Magnetic Particle Examination of Steel Forgings
A370 Test Methods and Definitions for Mechanical Testing of Steel Products
A388/A388M Practice for Ultrasonic Examination of Steel Forgings
A788/A788M Specification for Steel Forgings, General Requirements
E290 Test Methods for Bend Testing of Material for Ductility
E381 Method of Macroetch Testing Steel Bars, Billets,Blooms, and Forgings
3. Terminology
3.1 The terminology section of Specification A788/A788M is applicable to this specification.
3.2 Definitions of Terms Specific to This Standard:
3.2.1 class—a description of steel forgings based on heat treatment, mechanical properties and composition.
3.2.2 controlling cross section thickness (T C )—the diameter of the largest theoretical sphere which can be inscribed within the volume of the forging.
3.2.3 T P —designates prolongations which have a size other than the controlling cross section thickness (T C ).
4. Ordering Information and General Requirements
4.1 Material supplied to this specification shall conform to the requirements of Specification A788/A788M which outlines additional ordering information, manufacturing requirements,testing and retesting methods and procedures, marking,certification, product analysis variations and additional supplementary requirements.
4.1.1 If the requirements of this specification are in conflict with the requirements of Specification A788/A788M, the requirements of this specification shall prevail.
4.2 When this specification is to be applied to an inquiry,contract, or order, the purchaser should furnish the following information:
4.2.1 The ordering information required by Specification A788/A788M,
4.2.2 The class of forging desired as listed in Table 1,
4.2.3 Location(s) of areas of significant loading if test specimens are to be located in accordance with 7.1.4.5,
4.2.4 The options which may be selected as found in 5.3.2,6.1, and 7.3, and
4.2.5 Any applicable supplementary requirements.
5. Materials and Manufacture
5.1 Discard—Sufficient discard shall be made from each ingot to secure freedom from piping and undue segregation.
5.2 Forging Process:
5.2.1 The forging shall be brought as close as practical to finished shape and size by hot mechanical work.
5.2.2 Supplementary requirements S2, S14, and S15 may be specified by the purchaser to satisfy concerns about the utility of the proposed forging.
5.3 Heat Treatment:
5.3.1 All forgings, other than Class A, shall be heat treated.See Section 7.
5.3.2 Where options exist within a class, the choice of heat treatment shall be left to the discretion of the manufacturer,unless the purchaser specifies one of the available options.
6. Chemical Composition
6.1 The steel shall conform to the requirements prescribed in Table 1.
TABLE 1 Chemical Requirements
Elements | Composition, max, % | |
Classes A to F and AH to FH |
Classes G to N and GH to NH |
|
Manganese | 1.35 | ... |
Phosphorus | 0.050 | 0.040 |
Sulfur | 0.025 | 0.025 |
6.2 The choice of chemical composition is left to the discretion of the manufacturer, unless otherwise specified by the purchaser. See Appendix X2.
6.3 Heat Analysis:
6.3.1 An analysis of each heat shall be made by the manufacturer.
6.4 Product Analysis—An analysis may be made by the purchaser according to the requirements of Specification A788/A788M. If a standard grade has been used to manufacture the forging the permissible variations in composition of Specification A788/A788M shall apply. If a non-standard grade of steel has been used, and composition limits have not been supplied, the product analysis can be used only to confirm the type of steel supplied.
7. Mechanical Properties
7.1 Tensile Requirements:
7.1.1 The material shall conform to the tensile properties prescribed in Table 2. See Test Methods A370.
TABLE 2 Tensile Requirements A,B
A Forgings with controlling cross section thickness (T C ) in excess of 20 in. [508 mm] for all classes other than class D may be certified to Specification A668/A668M provided they meet the requirements for controlling cross sections of 20 in. [508 mm] listed in Table 2. Alternatively, the manufacturer and purchaser may agree upon the required mechanical property values as described in Supplement S9.1.
B Requirements presented in Table 2 are to be met at the test locations given in 7.1.4. Tests from other locations may not exhibit the property values shown in Table 2.
7.1.2 All Forgings—The dimensions of the controlling cross section thickness (T C ) of the forging at time of heat treatment determine the mechanical properties to be met within each class (see Table 2) except as noted in 7.1.4.2.
7.1.3 Number of Tests—Unless the purchaser specifies that forgings shall be furnished in accordance with the requirements of 7.3, the number of tension tests performed shall be as follows:
7.1.3.1 For all classes of heat-treated forgings with as-heat treated weights (excluding test prolongations) less than 5000 lb [2250 kg] each, one test shall be made from each size classification represented in each heat in each annealing or normalizing charge, or from each size classification in each heat in each normalizing or quenching charge represented in each tempering charge. For untreated forgings (Class A)weighing less than 5000 lb [2250 kg] each, one test from each heat shall be made.
7.1.3.2 On all classes, for forgings with as-heat treated weights (excluding test prolongations) of 5000 lb [2250 kg] or more, at least one test from each forging shall be made.
7.1.3.3 On all classes, for forgings with as-heat treated weights (excluding test prolongations) of 7000 lb [3200 kg] or more, two tests will be taken: on ring and disk forgings 180° apart; on shafts and long hollow cylinders (over 80 in. [2.0 m] in length excluding test material), one from each end and offset 180°. Shafts and cylinder forgings 80 in. [2.0 m] or less in length (excluding test material) may have both tests located at one end 180° apart.
7.1.3.4 When forgings are made in multiple as a single forging, that is, forged as one piece and divided after heat treatment, the multiple forging shall be considered as one forging, and the number of tests required shall be as designated in 7.1.3.1, 7.1.3.2, and 7.1.3.3.
7.1.4 Prolongations:
7.1.4.1 A sufficient number of the forgings shall have prolongations for extracting specimens for testing. Examples of test locations for various forging configurations are shown in Figs. 1 and 2.
FIG. 1 Examples of Locations of Test Specimens for Various Types of Forgings (see Note 1).
FIG. 2 Examples of Locations of Test Specimens for Various Types of Forgings (see Note 1).
NOTE 1—Figures provided demonstrate the concept of controlling cross section thickness (T C ) but do not encompass all possible test prolongation configurations which meet the requirements of Section 7.
7.1.4.2 For all forgings of non-uniform cross section in classes A, B, C, D, E, G and H: The prolongation(s) may be extensions of sections other than the controlling cross section thickness (T C ), that is T P ≠ T C . In this case, the dimension of T P shall determine the mechanical properties to be met within each class. When T P ≠ T C , T P shall not have more reduction than the smallest cross section to be qualified.
(1) For annealed, normalized, or normalized and tempered forgings in classes A, B, C, D, E, G and H the center of the gage length axis of tension test specimens shall be 1 ⁄ 4 the controlling cross section thickness (T C ) from one surface except as noted in 7.1.4.2 (2).
(2) If the prolongation thickness (T P ) is less than the controlling cross section thickness (T C ) the center of the gage length axis of the tension test shall be ¼ of the prolongation thickness (T P ) from one surface.
7.1.4.3 For quenched forgings in Classes F, J, K, L, M, and N, the center of the gage length axis of the tension test specimen shall be at a minimum 1 ⁄ 4 (T C ) from one quenched surface and 3 1 ⁄ 2 in. [90 mm] from all other quenched surfaces.
7.1.4.4 In place of prolongations, the manufacturer may: (1) elect to submit a representative forging(s) to represent each test lot; in this event, the representative forging must be made from the same heat of steel, must not receive more reduction than the forging it represents, must receive the same type of hot working it represents, be of the same controlling cross section thickness (T C ), and have been heat treated in the same furnace charge as the forging(s) it represents; or (2) obtain the test specimen from the trepanned material of transverse or radial holes, provided the required depth is met.
7.1.4.5 With prior purchaser approval, test specimens may be taken at a depth (t) corresponding to the distance from the area of significant stress to the nearest heat treated surface and at least twice this distance (2t) from any second surface.However, the test depth shall not be nearer to one heat-treated surface than 3 ⁄ 4 in. [19 mm] and to the second heat treated surface than 1 1 ⁄ 2 in. [38 mm]. Sketches showing the exact test locations shall be approved by the purchaser when this method is used.
7.1.5 Tests for acceptance shall be made after final heat treatment of the forgings. Thermal cycling after mechanical testing is complete shall not exceed 50°F [30°C] less than the temperature used to establish mechanical properties.
7.1.6 Test specimen orientation relative to the axis of major metal flow is to be at the discretion of the manufacturer provided the requirements of Table 2 are met. Test specimen orientation shall be reported.
7.1.7 Yield point shall be determined on carbon steel Grades Athrough F, and yield strength on alloy steel Grades G through N. For carbon steel grades not showing a yield point, the yield strength at 0.2 % offset shall be reported.
7.2 Hardness Tests—Brinell hardness tests shall be performed after heat treatment (except on Class A forgings) and rough machining on each forging weighing under 7000 lb [3200 kg] at the time of heat treatment and each multiple forging made in accordance with 7.1.3.3 weighing under 7000 lb [3200 kg] at the time of heat treatment.
7.2.1 Hardness testing on forgings in excess of 7000 lb [3200 kg] at the time of heat treatment may be omitted provided they meet the tensile requirements of Table 2. For additional exceptions see 7.1.3.4 and 7.3.
7.2.2 When ordered without rough machining, hardness measurements shall be conducted on the forgings after heat treatment. Due consideration should be provided for the removal of oxidation and decarburization to ensure accuracy of hardness results when forgings which have not been rough machined are evaluated.
7.2.3 The average value of the hardness readings on each forging shall fall within the hardness ranges specified in Table 2. The permissible variation in hardness in any forging over 250 lb [110 kg] shall not exceed 30 HBW for ClassesAthrough E, 40 HB for Classes F through J, 50 HB for Classes K through N.
7.2.4 At least two hardness tests shall be taken on each flat face of disks, rings, and hollow forgings over 250 lb [110 kg] approximately at mid-radius and 180° apart, for example, at the 3:00 and 9:00 positions on one face, and 6:00 and 12:00 positions on the opposite face. On solid forgings over 250 lb [110 kg], at least four tests shall be taken on the periphery of the forging, two at each end 180° apart.
7.2.5 For forgings 250 lb [110 kg] and less, Brinell testing shall be performed on the broken test specimens representing the heat or heats included in each heat treating charge, or in the case of untreated forgings (Class A), on the test specimen representing each heat. The results shall meet the requirements of Table 2. If the purchaser desires Brinell testing of each forging, Supplementary Requirement S11 may be used.
7.3 If so specified by the purchaser, forgings may be supplied on the basis of hardness tests alone. If this option is exercised, the class shall be identified in certification and marking with the suffix “H,” that is, “AH,” “BH,” “CH,” etc.
8. Retreatment
8.1 When heat-treated forgings are specified, and the mechanical test results of any test lot do not conform to the requirements specified, the manufacturer may re-austenitize the lot not more than three additional times, and retests shall be made according to Section 7. Multiple retempering is not precluded by this requirement.
8.2 When untreated forgings (ClassA) are specified, and the mechanical test results of any test lot do not conform to the requirements specified, the manufacturer may anneal,normalize, or normalize and temper, one or more times, but not more than three times; and retests shall be made in accordance with Section 7. The tensile properties shall conform to the requirements for the class of forgings ordered (Class A).
9. Inspection, Rejection, and Certification
9.1 Facilities for inspection at the place of manufacture,rejection of forgings and certification shall comply with Specification A788/A788M.
10. Product Marking
10.1 The marking requirements of Specification A788/A788M shall be augmented as follows.
10.2 Each forging over 250 lb [110 kg] shall be legibly stamped by the manufacturer with the manufacturer’s name or trademark, the manufacturer’s serial number, the specification identification number, followed by the appropriate class number and, where applicable, a standard Grade designation.
10.3 For forgings 250 lb [110 kg] and under, the purchaser may indicate the nature and location of identification marks.
10.4 The type of stamps to be used shall be round-nosed or “interrupted-dot” die stamps having a minimum radius of 1 ⁄ 32
in. [0.79 mm].
11. Keywords
11.1 alloy steel forgings; carbon steel forgings; general industrial applications; heat treatment classifications; strength classifications