ISO 8535-1 Steel tubes for high-pressure fuel injection pipe
ISO 8535-1 Diesel engines — Steel tubes for high-pressure fuel injection pipes —Part 1:Requirements for seamless cold-drawn single-wall tubes
1 Scope
This part of ISO 8535 specifies dimensions and requirements for seamless cold-drawn single-wall steel tubes for high-pressure fuel injection pipes used on diesel (compression-ignition) engines (class2) and for fuel injection pump testing (class 1).
It applies to diesel (compression-ignition) engines.
2 Normative references
The following referenced documents are indispensable for the application of this document. For dated references, only the edition cited applies. For undated references, the latest edition of the referenced document (including any amendments) applies.
ISO 404, Steel and steel products — General technical delivery requirements
ISO 6507-1, Metallic materials — Vickers hardness test — Part 1: Test method
ISO 6892, Metallic materials — Tensile testing at ambient temperature
ISO 12345, Diesel engines — Cleanliness assessment of fuel injection equipment
3 Dimensions and tolerances
3.1 Diameters
Recommended inside and outside diameters are given in Table 1. Other sizes may be used by agreement between supplier and purchaser.
Tolerances on inside and outside diameters shall be as follows: 1)
a) Inside diameter, d:
d u 4mm: ± 0,05 mm for class 2;
± 0,025 mm for class 1;
d > 4mm: ± 0,10 mm for class 2.
NOTE Classes 1 and 2 are explained in Clause 1.
b) Outside diameter, D, for classes 1 and 2:
D < 8 mm: ± 0,06 mm;
D W 8 mm: ± 0,10 mm.
c) Concentricity of the tube outside diameter relative to the inside diameter shall be proportional to the wall
thickness, as shown in Figure 1.
Key
D outside diameter
d inside diameter
t wall thickness
3.2 Length
Length and tolerances on length shall be by agreement between supplier and purchaser.
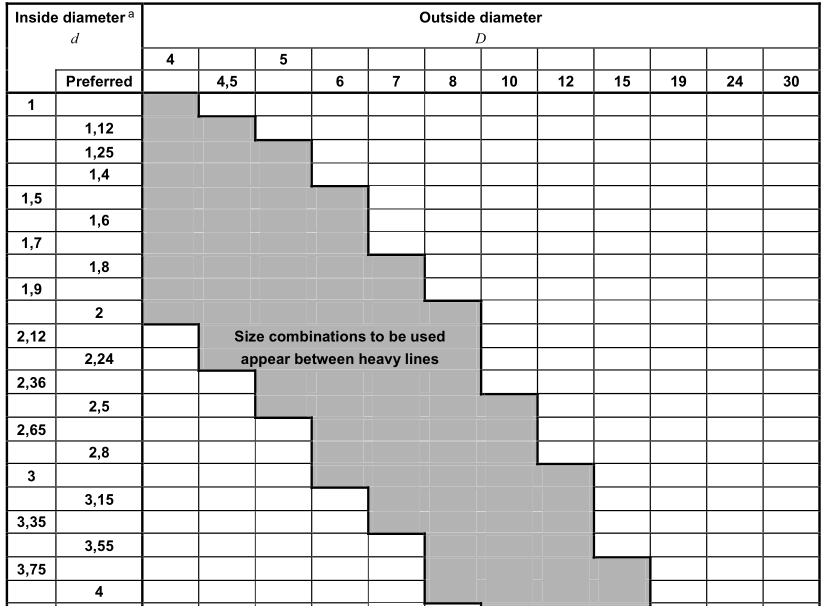
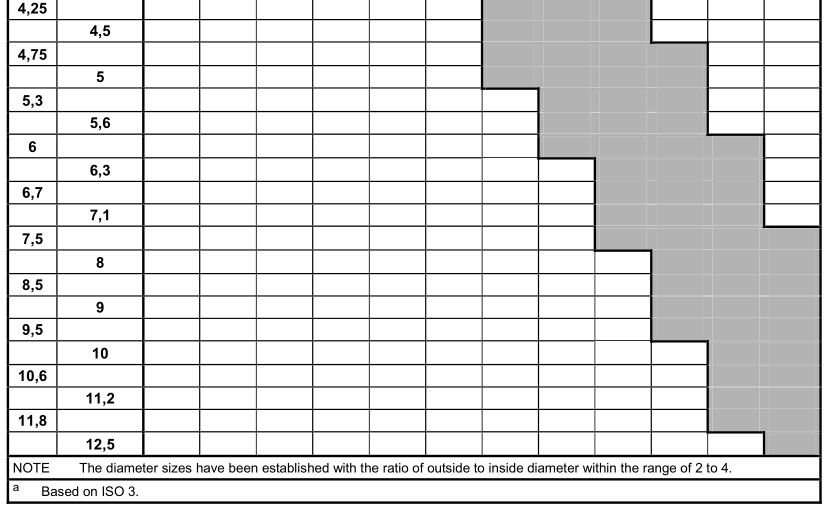
4 Material processing
4.1 Steel manufacturing process
The tubes shall be manufactured from unalloyed quality steel or an equivalent quality steel produced by a steel making process that ensures a very homogeneous structure.
If requested by the purchaser, the supplier shall state the method of manufacture and the deoxidation process used.
4.2 Manufacturing of tubes
The final reduction(s) of the tube shall be followed by heat treatment to achieve the specified mechanical properties.
4.3 Surface quality
4.3.1 General
The outside and inside surfaces of finished tubes shall be free from scale, rust, grooves, laps, laminations,deep pits or other injurious defects.
4.3.2 Minimum quality inside surface (bore grade S)
The inside of the tubes of bore grade S shall be finished to ensure a smooth bore of accurate size with no more than five imperfections (fissures, crevices, etc.) over 0,08 mm to 0,13 mm maximum deep, per tube cross-section, using × 50 magnification for examination (see Table 2).
4.3.3 Higher quality inside surface (bore grades O, P, Q, R)
If closer control over the depth of imperfections is required, bore grades O, P, Q or R, assessed under the magnification indicated (see Table 2) may be specified in the tube designation (see Clause 6).
4.4 Surface finish
The outside surface of the tube may be coated on delivery by metal plating or galvanizing, or may be submitted to a chemical surface treatment (see Table 3).
The inside surface of the tube shall remain uncoated.
4.5 Minimum mechanical properties of tubes
The tubes shall comply with one of the classes of mechanical properties (codes 1 to 3) as listed in Table 4.
4.6 Cleanliness
The bore shall be clean and free from any contamination or coating which would impair the processing and serviceability of the tubes. When specifying a cleanliness requirement for the inside of the tubes, ISO 12345 shall be used.
4.7 Straightness
Unless otherwise agreed between supplier and purchaser, the tubes shall be straight within a maximum error of 1 in 400 with no localized deformation.
4.8 Corrosion-resistance
The outside and inside surfaces shall be protected against corrosion for transportation and storage in closed areas. A permanent coating may be used on the outside surface when agreed between supplier and purchaser. Any temporary coating used shall not be injurious to the injection and combustion systems of engine and shall be removable with diesel fuel.
5 Testing
5.1 General
Unless otherwise agreed between supplier and purchaser, tests shall be carried out in accordance with 5.2 to 5.8.
5.2 Scope of tests
Tubes shall be tested by lots of the same dimensions, steel type, heat treatment and surface finish. Tubes from each heat of steel shall be tested irrespective of lot.
For the test in 5.4, a test inspector shall select one tube from each lot ,and for the test in 5.6, three tubes. The tests in 5.3, 5.7.1 and 5.8 shall be performed on all selected tubes.
For the test in 5.7.3, the lot size, the number of samples and the acceptance limit shall be agreed upon between supplier and purchaser.
5.3 Dimension tests
The tube dimension shall comply with the dimensions and tolerances indicated in Clause 3.
5.4 Mechanical property tests
The tubes shall comply with the specifications given in Table 4. The tests shall be made in accordance with ISO 6892 and ISO 6507-1. Tensile strength, yield stress, elongation and hardness shall be measured.
5.5 Bending test
The tube shall withstand cold bending through 180° over a rod of the same diameter as the tube outside diameter, without showing other than outside superficial cracks.
5.6 Cold upsetting of tubes
This test shall be carried out on tubes of outside diameter 15 mm and below.
A length of tube twice the outside diameter (2D) shall be capable of being compressed to a length D without showing cracks of depths exceeding 0,13 mm.
The test shall be made between two plane and parallel plates in a suitable fixture.
5.7 Surface quality test
5.7.1 A visual check shall be made to ensure that tubes satisfy the requirements in 4.3.1.
5.7.2 If mutually agreed between supplier and purchaser, the visual inspection may be replaced by a non-destructive test procedure.
5.7.3 If a proof of a specified defect depth in the bore is required, an inspection by attributes, with an agreed Acceptable Quality Level (AQL) shall be set when ordering; the test shall be made on metallographic cross-sections of the tube with the minimum magnification specified in Table 2.
5.7.4 Surface coatings on tubes with plated or otherwise treated surfaces shall satisfy tests on these coatings when required. Such tests shall be agreed between supplier and purchaser.
5.8 Inside pressure test
Tubes shall be capable of withstanding appropriate inside pressure which shall be agreed between supplier and purchaser (see Annex A), without permanent internal deformation or burst. This ability shall be confirmed by a hydraulic test. Other non-destructive tests, such as electronic testing, may be used if agreed between supplier and purchaser.
5.9 Retesting
If, after testing in accordance with 5.4, the selected tube fails, two other tubes shall be taken from the same lot to repeat the test. The same procedure shall apply to the test in 5.6. Each of the tubes taken shall meet the test requirements. If any tube fails the test requirements, the whole lot is considered as rejected.
The supplier may submit a rejected lot for acceptance again in an improved condition, e.g. by repeating the heat treatment.
If, in this case, the test results of 5.4 and 5.6 do not fulfil the requirements, the whole lot shall be rejected.
5.10 Test certificate
A test certificate, if required [see 6 i)], shall be issued for each shipment, confirming that the tubes supplied meet the specifications of this part of ISO 8535. For proof, the records of the continuous production inspections concerning the following tests may be used:
a) dimensions according to 5.3;
b) mechanical properties according to 5.4;
c) bending test according to 5.5;
d) cold upsetting according to 5.6;
e) visual inspection according to 5.7.1;
f) metallographic test according to 5.7.3;
g) inside pressure test according to 5.8.
Other test certificates may be agreed upon between supplier and purchaser.
6 Designation
A steel tube that meets the requirements of this part of ISO 8535 shall be designated as follows, in the order given:
a) the word “Tube”;
b) reference to this part of ISO 8535;
c) tube type: a seamless cold-drawn single-wall steel tube is indicated by the letter “S”;
d) size: the second and third characters identify the nominal inside and outside diameters respectively of the
tube, in millimetres;
e) class: the fourth character determines the bore tolerance [see 3.1 a)];
f) the fifth character identifies the mechanical properties of the tube in accordance with Table 4;
g) the sixth character identifies the bore grade of the tube in accordance with Table 2;
h) the seventh character identifies the treatment of the outside surface of the tube (see Table 3);
i) at the end the of the designation, the letter “Z” may be added to indicate that a certificate from the tube manufacturer is required for confirmation of compliance with this part of ISO 8535 and additional delivery requirements, if any (see ISO 404).
7 Identification and marking
Tubes shall be identified by use of labels with the designation according to Clause 6. Additional marking is permissible if agreed between supplier and purchaser.
8 Packing
Unless otherwise agreed upon between supplier and purchaser, the tubes shall be delivered in secure bundles, with tubes sealed at both ends.
1 Scope
This part of ISO 8535 specifies dimensions and requirements for seamless cold-drawn single-wall steel tubes for high-pressure fuel injection pipes used on diesel (compression-ignition) engines (class2) and for fuel injection pump testing (class 1).
It applies to diesel (compression-ignition) engines.
2 Normative references
The following referenced documents are indispensable for the application of this document. For dated references, only the edition cited applies. For undated references, the latest edition of the referenced document (including any amendments) applies.
ISO 404, Steel and steel products — General technical delivery requirements
ISO 6507-1, Metallic materials — Vickers hardness test — Part 1: Test method
ISO 6892, Metallic materials — Tensile testing at ambient temperature
ISO 12345, Diesel engines — Cleanliness assessment of fuel injection equipment
3 Dimensions and tolerances
3.1 Diameters
Recommended inside and outside diameters are given in Table 1. Other sizes may be used by agreement between supplier and purchaser.
Tolerances on inside and outside diameters shall be as follows: 1)
a) Inside diameter, d:
d u 4mm: ± 0,05 mm for class 2;
± 0,025 mm for class 1;
d > 4mm: ± 0,10 mm for class 2.
NOTE Classes 1 and 2 are explained in Clause 1.
b) Outside diameter, D, for classes 1 and 2:
D < 8 mm: ± 0,06 mm;
D W 8 mm: ± 0,10 mm.
c) Concentricity of the tube outside diameter relative to the inside diameter shall be proportional to the wall
thickness, as shown in Figure 1.
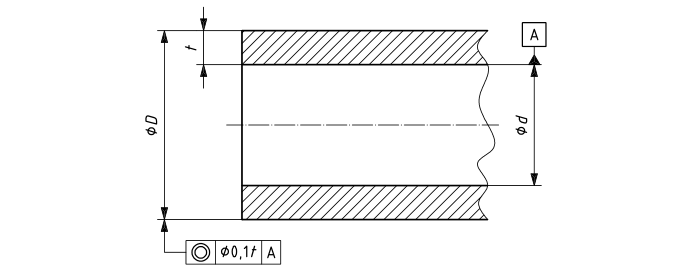
Key
D outside diameter
d inside diameter
t wall thickness
Figure 1 — Concentricity of the tube outside diameter
3.2 Length
Length and tolerances on length shall be by agreement between supplier and purchaser.
Table 1 — Recommended inside and outside diameters Dimensions in millimetres
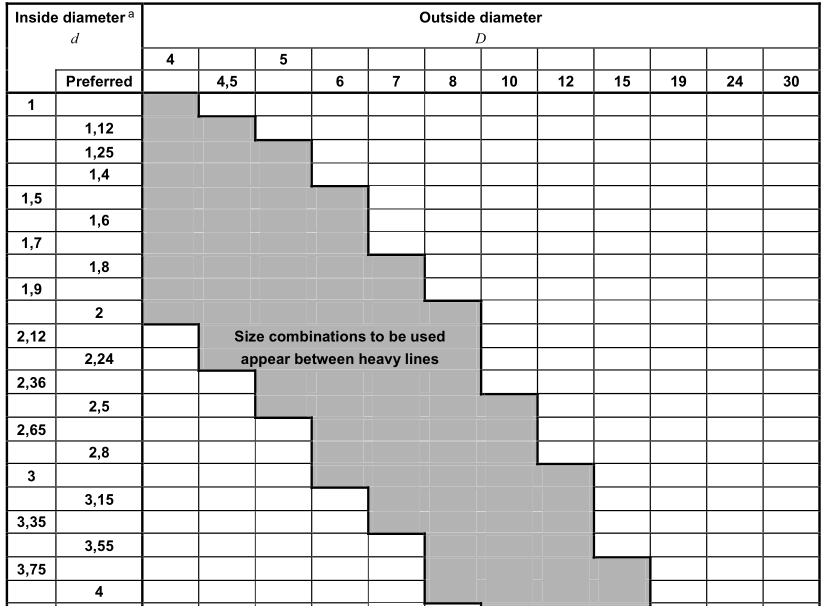
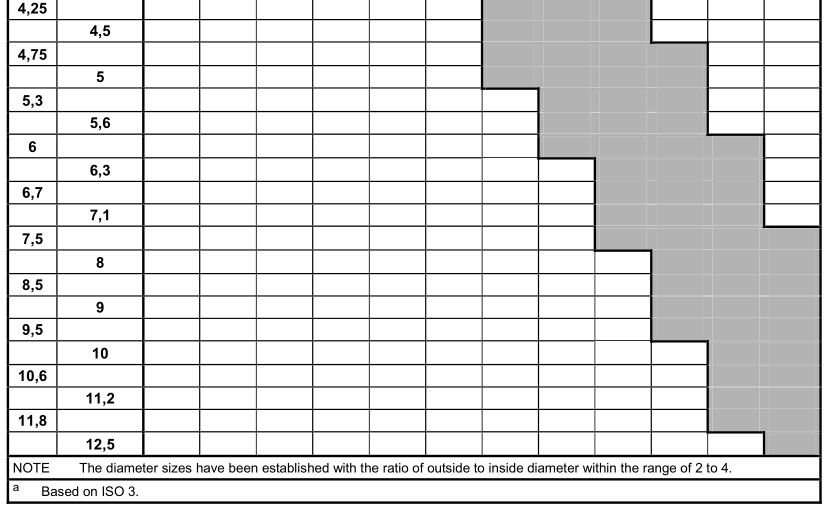
4 Material processing
4.1 Steel manufacturing process
The tubes shall be manufactured from unalloyed quality steel or an equivalent quality steel produced by a steel making process that ensures a very homogeneous structure.
If requested by the purchaser, the supplier shall state the method of manufacture and the deoxidation process used.
4.2 Manufacturing of tubes
The final reduction(s) of the tube shall be followed by heat treatment to achieve the specified mechanical properties.
4.3 Surface quality
4.3.1 General
The outside and inside surfaces of finished tubes shall be free from scale, rust, grooves, laps, laminations,deep pits or other injurious defects.
4.3.2 Minimum quality inside surface (bore grade S)
The inside of the tubes of bore grade S shall be finished to ensure a smooth bore of accurate size with no more than five imperfections (fissures, crevices, etc.) over 0,08 mm to 0,13 mm maximum deep, per tube cross-section, using × 50 magnification for examination (see Table 2).
4.3.3 Higher quality inside surface (bore grades O, P, Q, R)
If closer control over the depth of imperfections is required, bore grades O, P, Q or R, assessed under the magnification indicated (see Table 2) may be specified in the tube designation (see Clause 6).
Table 2 — Bore grades
Code | Permitted imperfections | Magnification |
S | As in 4.3.2 | × 50 |
R | A maximum of five imperfections over 0,05 mm to 0,08 mm maximum deep | × 100 |
Q | A maximum of five imperfections over 0,02 mm to 0,05 mm maximum deep | × 100 |
P | A maximum of five imperfections over 0,01 mm to 0,02 mm maximum deep | × 200 |
O | All imperfections equal to or less than 0,01 mm deep | × 500 |
4.4 Surface finish
The outside surface of the tube may be coated on delivery by metal plating or galvanizing, or may be submitted to a chemical surface treatment (see Table 3).
The inside surface of the tube shall remain uncoated.
Table 3 — Surface finish on delivery
Code | Outside surface condition | Application remarks |
0 | Not specified (at manufacturer’s choice). |
May have additional finish at manufacturer’s choice. |
1 |
Outside surface as-processed, without any additional finish. Tubes annealed or normalized in a controlled atmosphere may be discoloured, but shall be free from loose scale. |
Condition preferred for further surface processing. |
2 |
Zinc electroplated with a coating layer thickness of 8 µm minimum and an additional colourless chromating a . |
When minimum corrosion-resistance is required. Not recommended for use with light alcohol-based fuels such as methanol. |
3 |
Zinc electroplated with a coating layer thickness of 8 µm minimum and an additional yellow chromating a . |
|
(4,5,6,7,8) | (Reserved for further application). | |
9 | As specified subject to agreement. | |
a Chromating as described in ISO 2080 and ISO 4520. |
4.5 Minimum mechanical properties of tubes
The tubes shall comply with one of the classes of mechanical properties (codes 1 to 3) as listed in Table 4.
Table 4 — Mechanical properties
Code |
Minimum tensile Strength R m N/mm 2 |
Minimum upper yield Stress R eH N/mm 2 |
Minimum elongation A 5 % |
Maximum hardness HV |
1 | 310 | 205 | 30 | 115 |
2 | 360 | 220 | 23 | 150 |
3 | 490 | 355 | 22 | 194 |
NOTE The mechanical properties apply when the tube is tested in accordance with ISO 6507-1 and ISO 6892 |
4.6 Cleanliness
The bore shall be clean and free from any contamination or coating which would impair the processing and serviceability of the tubes. When specifying a cleanliness requirement for the inside of the tubes, ISO 12345 shall be used.
4.7 Straightness
Unless otherwise agreed between supplier and purchaser, the tubes shall be straight within a maximum error of 1 in 400 with no localized deformation.
4.8 Corrosion-resistance
The outside and inside surfaces shall be protected against corrosion for transportation and storage in closed areas. A permanent coating may be used on the outside surface when agreed between supplier and purchaser. Any temporary coating used shall not be injurious to the injection and combustion systems of engine and shall be removable with diesel fuel.
5 Testing
5.1 General
Unless otherwise agreed between supplier and purchaser, tests shall be carried out in accordance with 5.2 to 5.8.
5.2 Scope of tests
Tubes shall be tested by lots of the same dimensions, steel type, heat treatment and surface finish. Tubes from each heat of steel shall be tested irrespective of lot.
For the test in 5.4, a test inspector shall select one tube from each lot ,and for the test in 5.6, three tubes. The tests in 5.3, 5.7.1 and 5.8 shall be performed on all selected tubes.
For the test in 5.7.3, the lot size, the number of samples and the acceptance limit shall be agreed upon between supplier and purchaser.
5.3 Dimension tests
The tube dimension shall comply with the dimensions and tolerances indicated in Clause 3.
5.4 Mechanical property tests
The tubes shall comply with the specifications given in Table 4. The tests shall be made in accordance with ISO 6892 and ISO 6507-1. Tensile strength, yield stress, elongation and hardness shall be measured.
5.5 Bending test
The tube shall withstand cold bending through 180° over a rod of the same diameter as the tube outside diameter, without showing other than outside superficial cracks.
5.6 Cold upsetting of tubes
This test shall be carried out on tubes of outside diameter 15 mm and below.
A length of tube twice the outside diameter (2D) shall be capable of being compressed to a length D without showing cracks of depths exceeding 0,13 mm.
The test shall be made between two plane and parallel plates in a suitable fixture.
5.7 Surface quality test
5.7.1 A visual check shall be made to ensure that tubes satisfy the requirements in 4.3.1.
5.7.2 If mutually agreed between supplier and purchaser, the visual inspection may be replaced by a non-destructive test procedure.
5.7.3 If a proof of a specified defect depth in the bore is required, an inspection by attributes, with an agreed Acceptable Quality Level (AQL) shall be set when ordering; the test shall be made on metallographic cross-sections of the tube with the minimum magnification specified in Table 2.
5.7.4 Surface coatings on tubes with plated or otherwise treated surfaces shall satisfy tests on these coatings when required. Such tests shall be agreed between supplier and purchaser.
5.8 Inside pressure test
Tubes shall be capable of withstanding appropriate inside pressure which shall be agreed between supplier and purchaser (see Annex A), without permanent internal deformation or burst. This ability shall be confirmed by a hydraulic test. Other non-destructive tests, such as electronic testing, may be used if agreed between supplier and purchaser.
5.9 Retesting
If, after testing in accordance with 5.4, the selected tube fails, two other tubes shall be taken from the same lot to repeat the test. The same procedure shall apply to the test in 5.6. Each of the tubes taken shall meet the test requirements. If any tube fails the test requirements, the whole lot is considered as rejected.
The supplier may submit a rejected lot for acceptance again in an improved condition, e.g. by repeating the heat treatment.
If, in this case, the test results of 5.4 and 5.6 do not fulfil the requirements, the whole lot shall be rejected.
5.10 Test certificate
A test certificate, if required [see 6 i)], shall be issued for each shipment, confirming that the tubes supplied meet the specifications of this part of ISO 8535. For proof, the records of the continuous production inspections concerning the following tests may be used:
a) dimensions according to 5.3;
b) mechanical properties according to 5.4;
c) bending test according to 5.5;
d) cold upsetting according to 5.6;
e) visual inspection according to 5.7.1;
f) metallographic test according to 5.7.3;
g) inside pressure test according to 5.8.
Other test certificates may be agreed upon between supplier and purchaser.
6 Designation
A steel tube that meets the requirements of this part of ISO 8535 shall be designated as follows, in the order given:
a) the word “Tube”;
b) reference to this part of ISO 8535;
c) tube type: a seamless cold-drawn single-wall steel tube is indicated by the letter “S”;
d) size: the second and third characters identify the nominal inside and outside diameters respectively of the
tube, in millimetres;
e) class: the fourth character determines the bore tolerance [see 3.1 a)];
f) the fifth character identifies the mechanical properties of the tube in accordance with Table 4;
g) the sixth character identifies the bore grade of the tube in accordance with Table 2;
h) the seventh character identifies the treatment of the outside surface of the tube (see Table 3);
i) at the end the of the designation, the letter “Z” may be added to indicate that a certificate from the tube manufacturer is required for confirmation of compliance with this part of ISO 8535 and additional delivery requirements, if any (see ISO 404).
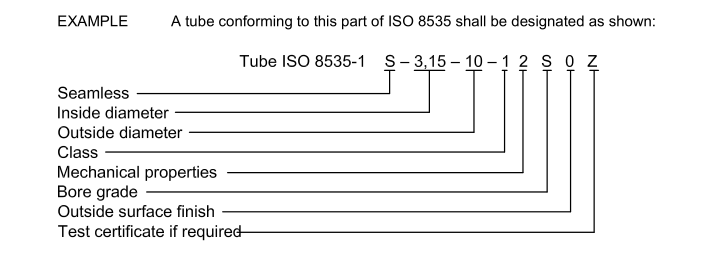
7 Identification and marking
Tubes shall be identified by use of labels with the designation according to Clause 6. Additional marking is permissible if agreed between supplier and purchaser.
8 Packing
Unless otherwise agreed upon between supplier and purchaser, the tubes shall be delivered in secure bundles, with tubes sealed at both ends.